Texturing Clay: An Accessible Method of Hardware
Hacking to Carve Clay with a Multifunctional CNC Machine
Imagine a ceramicist crafting a cup: they begin by taking a handful of clay, shaping it into a ball, wetting it with water, and using a pottery wheel to form the cup. Once partially dry, the artisan trims the edges using knifes and perhaps carves decorative patterns on the surface. After the cup is completely dry, it is coated with glaze and fired in a kiln and become the final cup. This requires the ceramicist to have a foundational understanding of the properties of clay, the skills of additive manufacturing (shaping) and subtractive manufacturing (refining), and knowledge of firing techniques. However, in transitioning to digital fabrication, the inherent complexity of these craft techniques is often simplified into two steps: computer-aided design and fabrication. And the comprehensive knowledge of the whole fabrication process is often overlooked.
Over the past 30 years, the user base for digital fabrication has significantly expanded. As ceramic craftsmanship transitions from handmade to digital, CNC machines like 3D printers and robotic arms have emerged as key tools. Craft and machine are not inherently at odds. A central question for those exploring ceramic production through digital fabrication is: How can digital clay fabrication highlight the material's diversity across the spectrum of practices? Moreover, how can it incorporate a comprehensive understanding of clay’s properties, manufacturing processes, and firing techniques?
This research investigates the integrated use of a multifunctional CNC machine to create clay surface textures, aiming to support accessible distributed manufacturing. Could combining multiple fabrication processes in digital workflows foster greater awareness of clay's diverse practices? Additionally, what new possibilities might emerge to deepen practitioners' engagement with the material?
Imagine a ceramicist crafting a cup: they begin by taking a handful of clay, shaping it into a ball, wetting it with water, and using a pottery wheel to form the cup. Once partially dry, the artisan trims the edges using knifes and perhaps carves decorative patterns on the surface. After the cup is completely dry, it is coated with glaze and fired in a kiln and become the final cup. This requires the ceramicist to have a foundational understanding of the properties of clay, the skills of additive manufacturing (shaping) and subtractive manufacturing (refining), and knowledge of firing techniques. However, in transitioning to digital fabrication, the inherent complexity of these craft techniques is often simplified into two steps: computer-aided design and fabrication. And the comprehensive knowledge of the whole fabrication process is often overlooked.
Over the past 30 years, the user base for digital fabrication has significantly expanded. As ceramic craftsmanship transitions from handmade to digital, CNC machines like 3D printers and robotic arms have emerged as key tools. Craft and machine are not inherently at odds. A central question for those exploring ceramic production through digital fabrication is: How can digital clay fabrication highlight the material's diversity across the spectrum of practices? Moreover, how can it incorporate a comprehensive understanding of clay’s properties, manufacturing processes, and firing techniques?
This research investigates the integrated use of a multifunctional CNC machine to create clay surface textures, aiming to support accessible distributed manufacturing. Could combining multiple fabrication processes in digital workflows foster greater awareness of clay's diverse practices? Additionally, what new possibilities might emerge to deepen practitioners' engagement with the material?
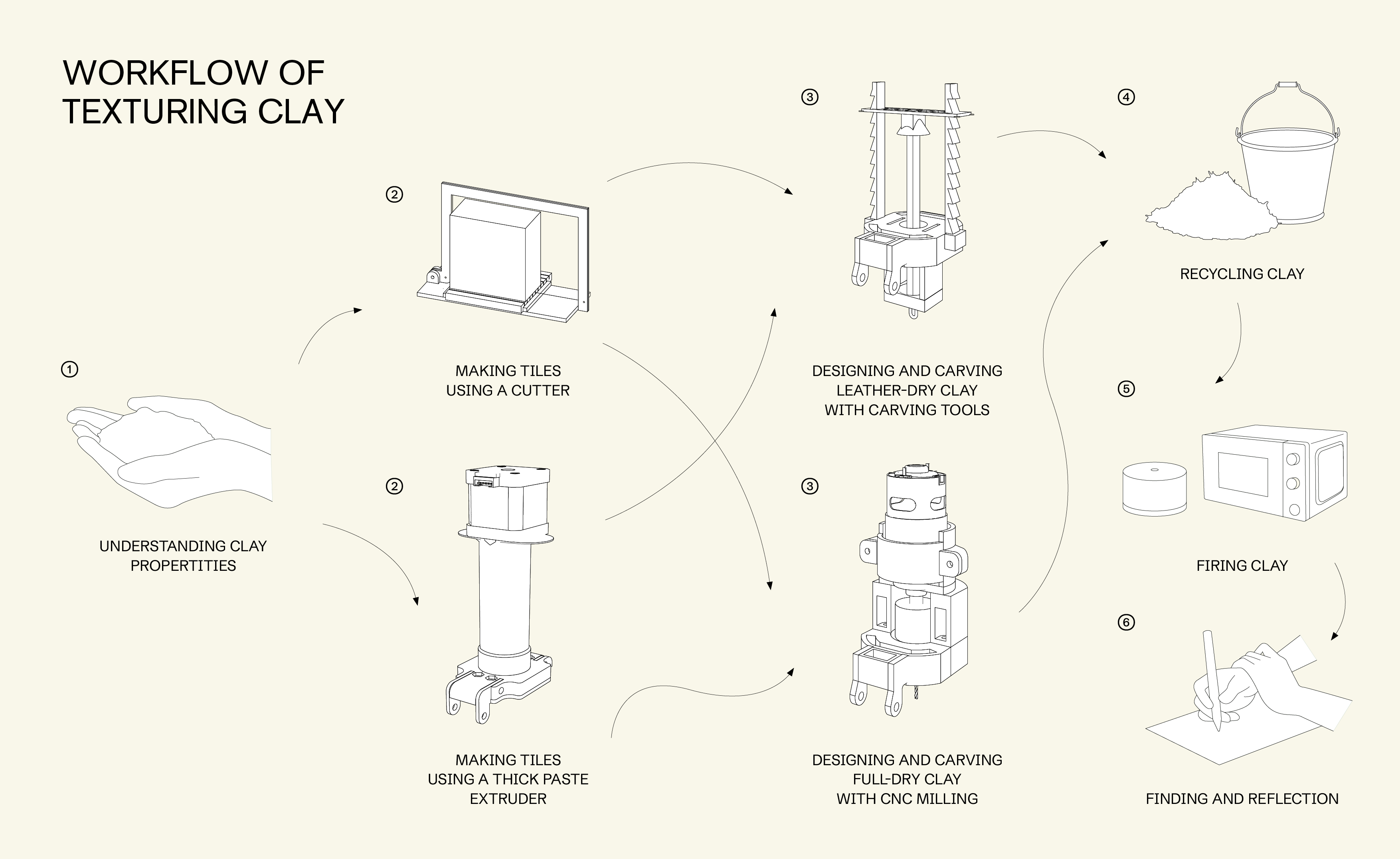
To facilitate a clearer understanding of
the foundational knowledge behind the digital manufacturing process for clay, the workflow is simplified it into the following diagram, including:
1. Understanding Clay Properties
2. Making Tiles
3. Designing and Carving
4. Recycling
5. Firing
6. Findings and Reflections.
For full explaination, check the booklet here.
The following session will focus on part of the content regarding tile making, carving and firing.
1. Understanding Clay Properties
2. Making Tiles
3. Designing and Carving
4. Recycling
5. Firing
6. Findings and Reflections.
For full explaination, check the booklet here.
The following session will focus on part of the content regarding tile making, carving and firing.
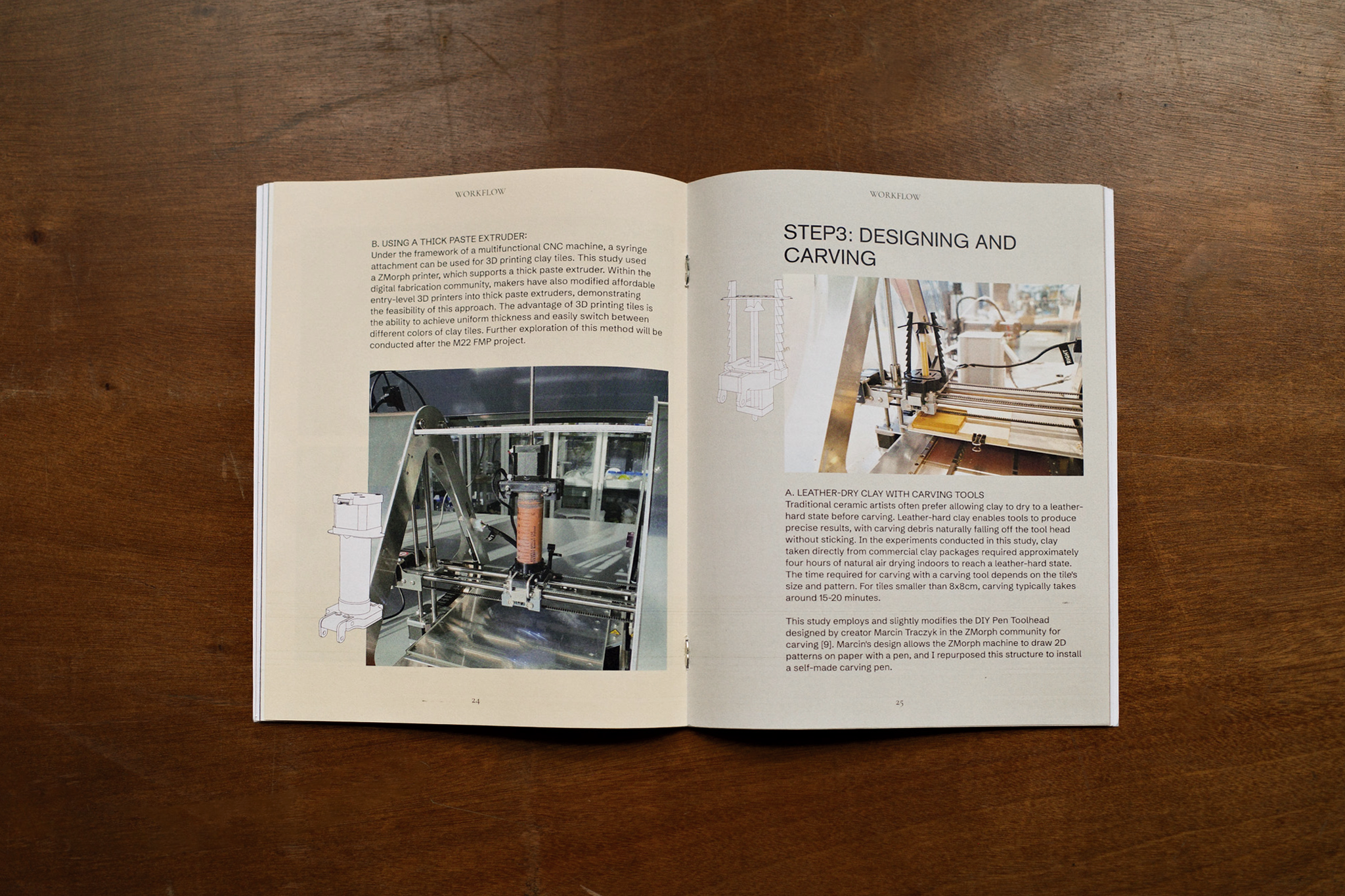

Making Tiles
a. Using a Cutter:
To create a clay cutter, tie a wire to small holes on a wooden frame, ensuring tension with wrapping or screws. To shape clay into blocks for cutting, this study used two L-shaped molds. Wrap the clay in plastic, assemble the molds, and repeatedly slam to form a block. Finally, cut with the clay cutter. A base mold with grooves can help ensure evenly spaced slabs.
b. Using a Thick Paste Extruder:
Using a syringe attachment on a multifunctional CNC machine, clay slabs can be 3D printed. The Zmorph machine supports a Thick Paste Extruder, and makers have modified entry-level 3D printers for this purpose, showing its feasibility. 3D printing ensures uniform slab thickness and easy color switching, with further exploration planned after the FMP(2025).
a. Using a Cutter:
To create a clay cutter, tie a wire to small holes on a wooden frame, ensuring tension with wrapping or screws. To shape clay into blocks for cutting, this study used two L-shaped molds. Wrap the clay in plastic, assemble the molds, and repeatedly slam to form a block. Finally, cut with the clay cutter. A base mold with grooves can help ensure evenly spaced slabs.
b. Using a Thick Paste Extruder:
Using a syringe attachment on a multifunctional CNC machine, clay slabs can be 3D printed. The Zmorph machine supports a Thick Paste Extruder, and makers have modified entry-level 3D printers for this purpose, showing its feasibility. 3D printing ensures uniform slab thickness and easy color switching, with further exploration planned after the FMP(2025).

Designing
Unlike traditional ceramists who use their hands and tools to carve directly into clay, digital fabrication machines rely on reading G-code to guide their movement for carving and milling. Inspired by MillPath, this study attempts to use Grasshopper to develop a design system that enables beginners to easily create and explore clay surface textures. The goal is to provide an accessible tool that balances the intuitiveness of design with the unique characteristics of handcrafted aesthetics.
Considering the dynamic possibilities between carving pens and carving movements, this study focuses on designing the machine's movement paths rather than the carving patterns themselves. Grasshopper, a flexible and visulaize software, is used as the design platform for this purpose.
Unlike traditional ceramists who use their hands and tools to carve directly into clay, digital fabrication machines rely on reading G-code to guide their movement for carving and milling. Inspired by MillPath, this study attempts to use Grasshopper to develop a design system that enables beginners to easily create and explore clay surface textures. The goal is to provide an accessible tool that balances the intuitiveness of design with the unique characteristics of handcrafted aesthetics.
Considering the dynamic possibilities between carving pens and carving movements, this study focuses on designing the machine's movement paths rather than the carving patterns themselves. Grasshopper, a flexible and visulaize software, is used as the design platform for this purpose.

Carving
a. Leather-dry Clay with Carving Tools:
Leather-dry clay allows clear carving, as scraps fall off without sticking. This study used and adapted Marcin Traczyk’s DIY Pen Toolhead from the Zmorph community for carving. The toolhead, originally designed for 2D pen drawings, was modified for custom carving, offering possibilities similar to traditional ceramicists' tools
a. Leather-dry Clay with Carving Tools:
Leather-dry clay allows clear carving, as scraps fall off without sticking. This study used and adapted Marcin Traczyk’s DIY Pen Toolhead from the Zmorph community for carving. The toolhead, originally designed for 2D pen drawings, was modified for custom carving, offering possibilities similar to traditional ceramicists' tools


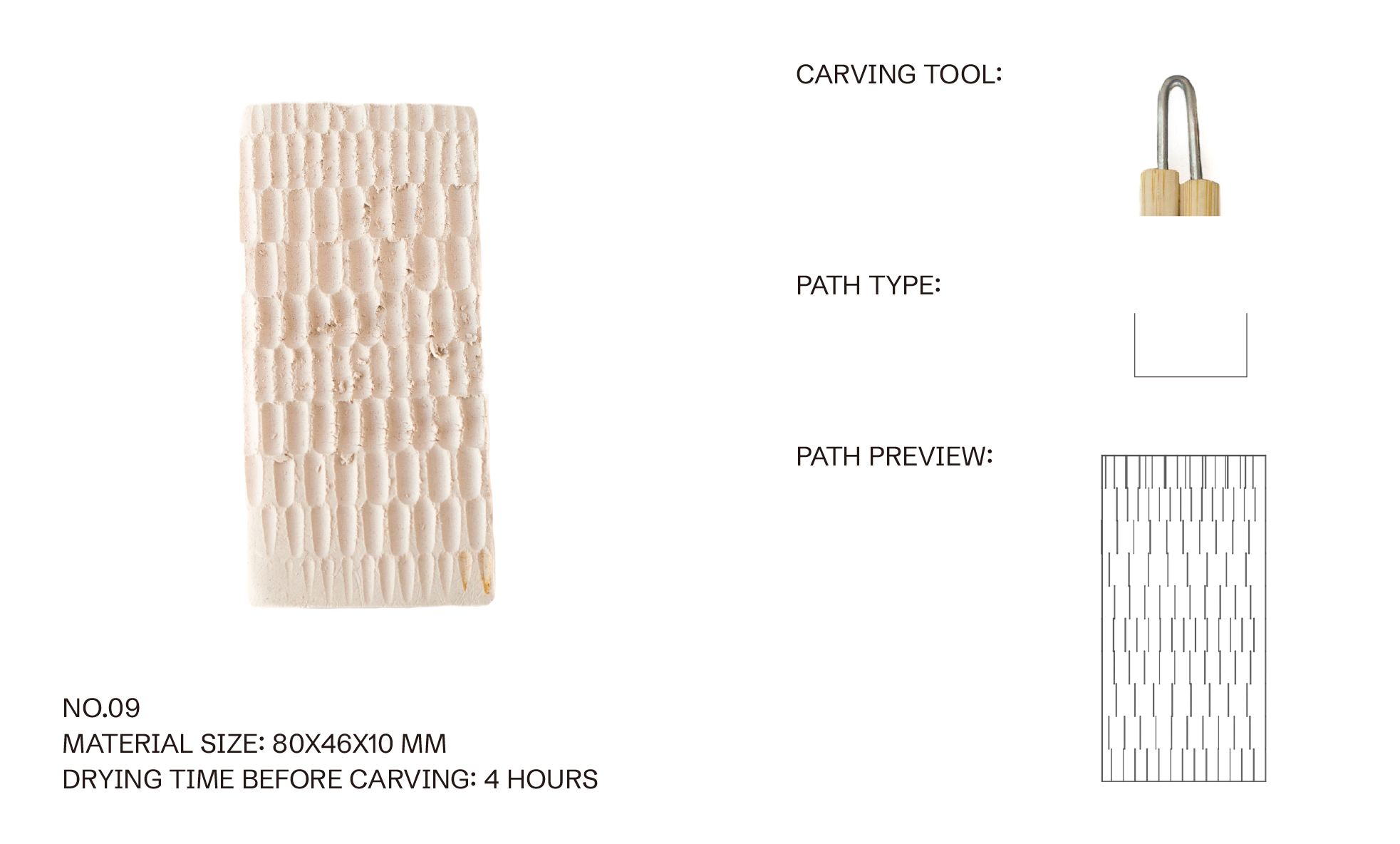
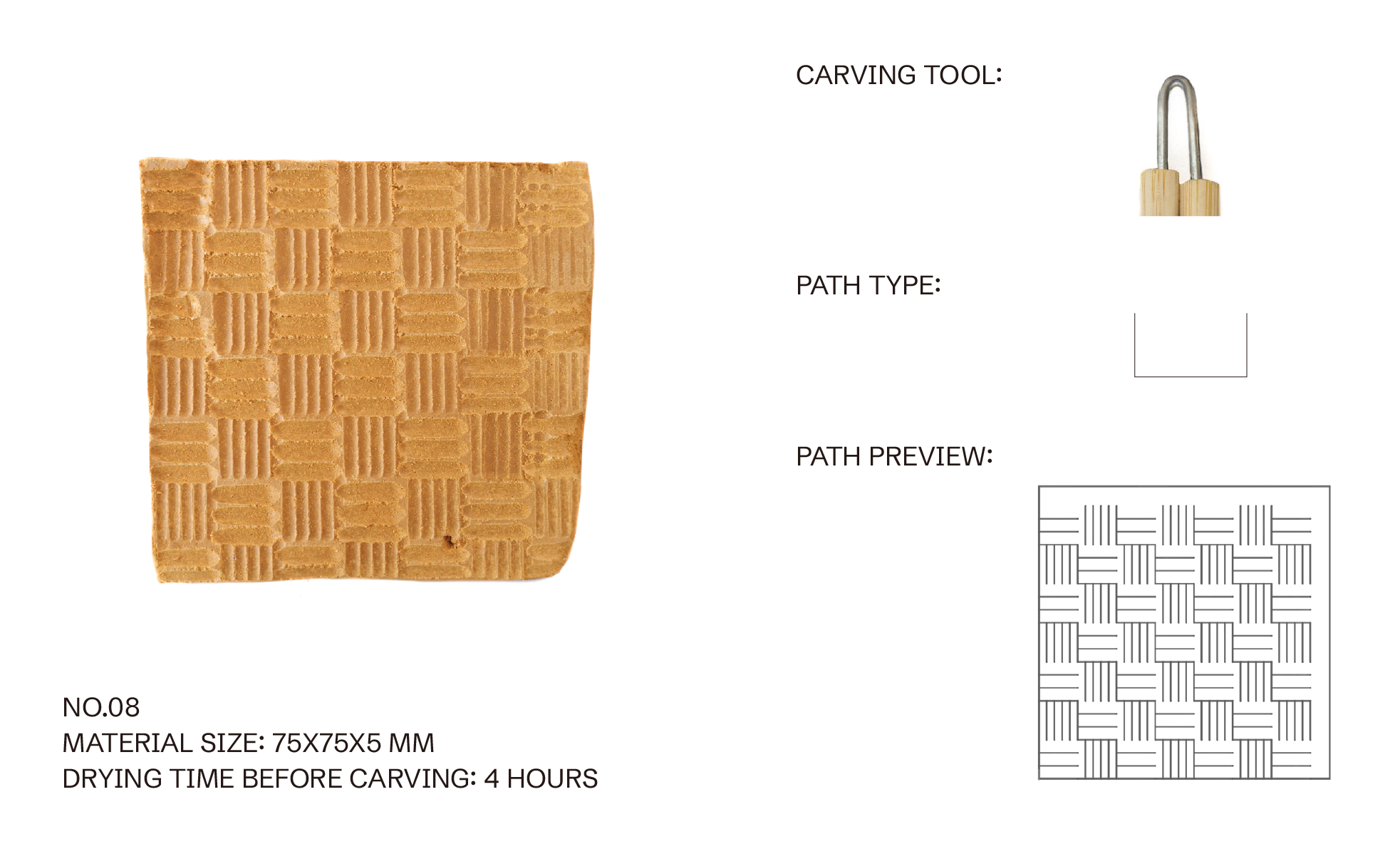
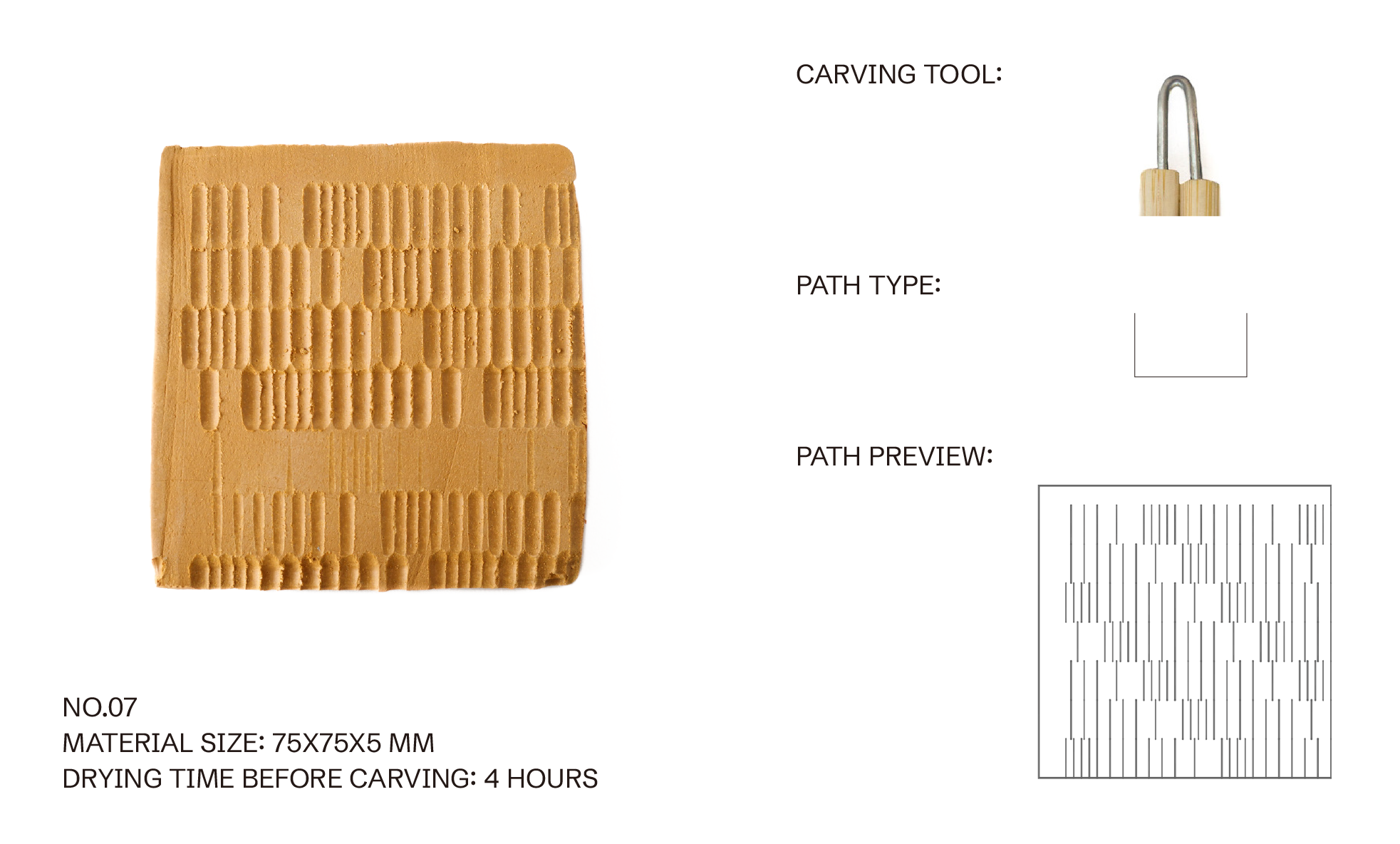
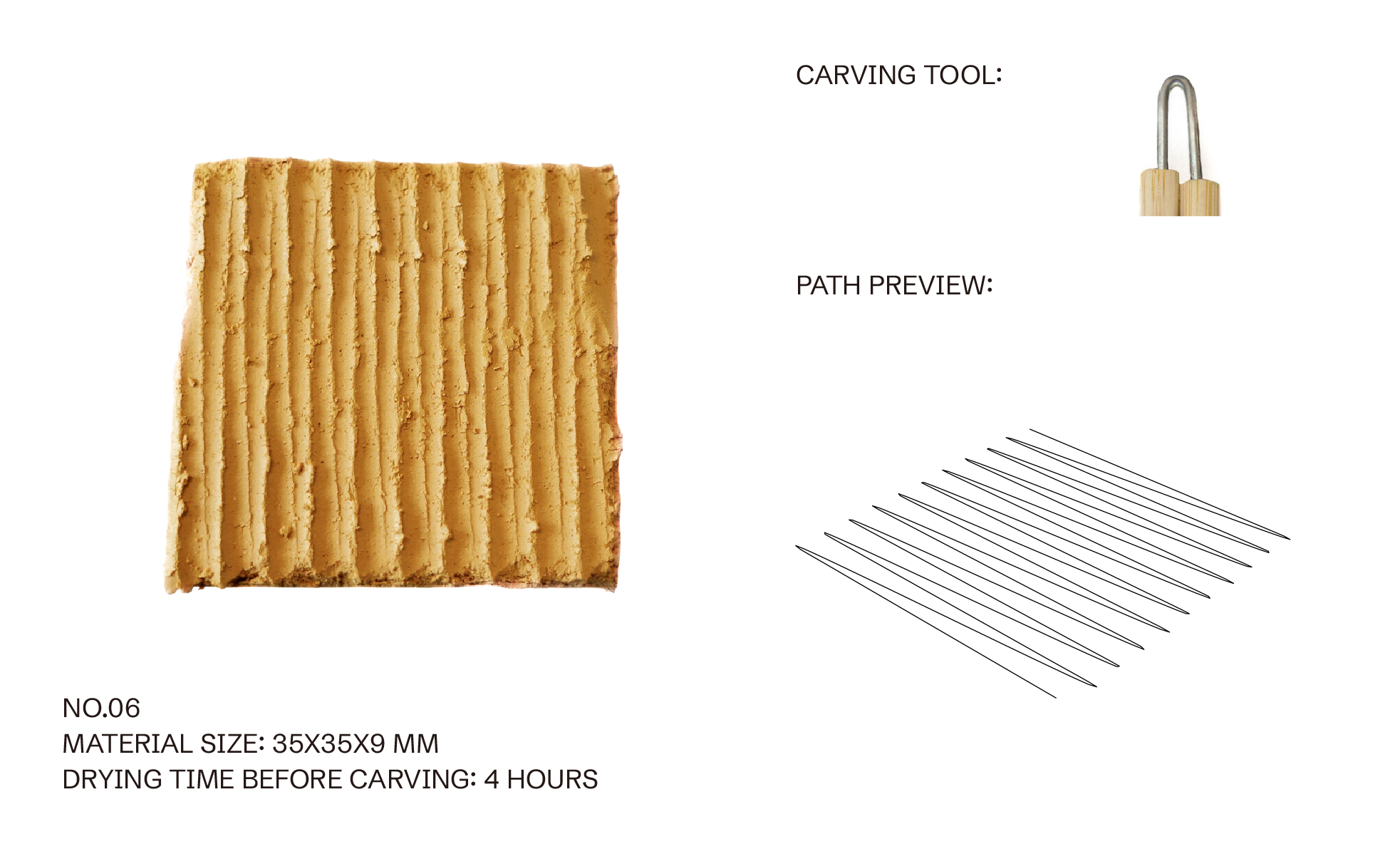



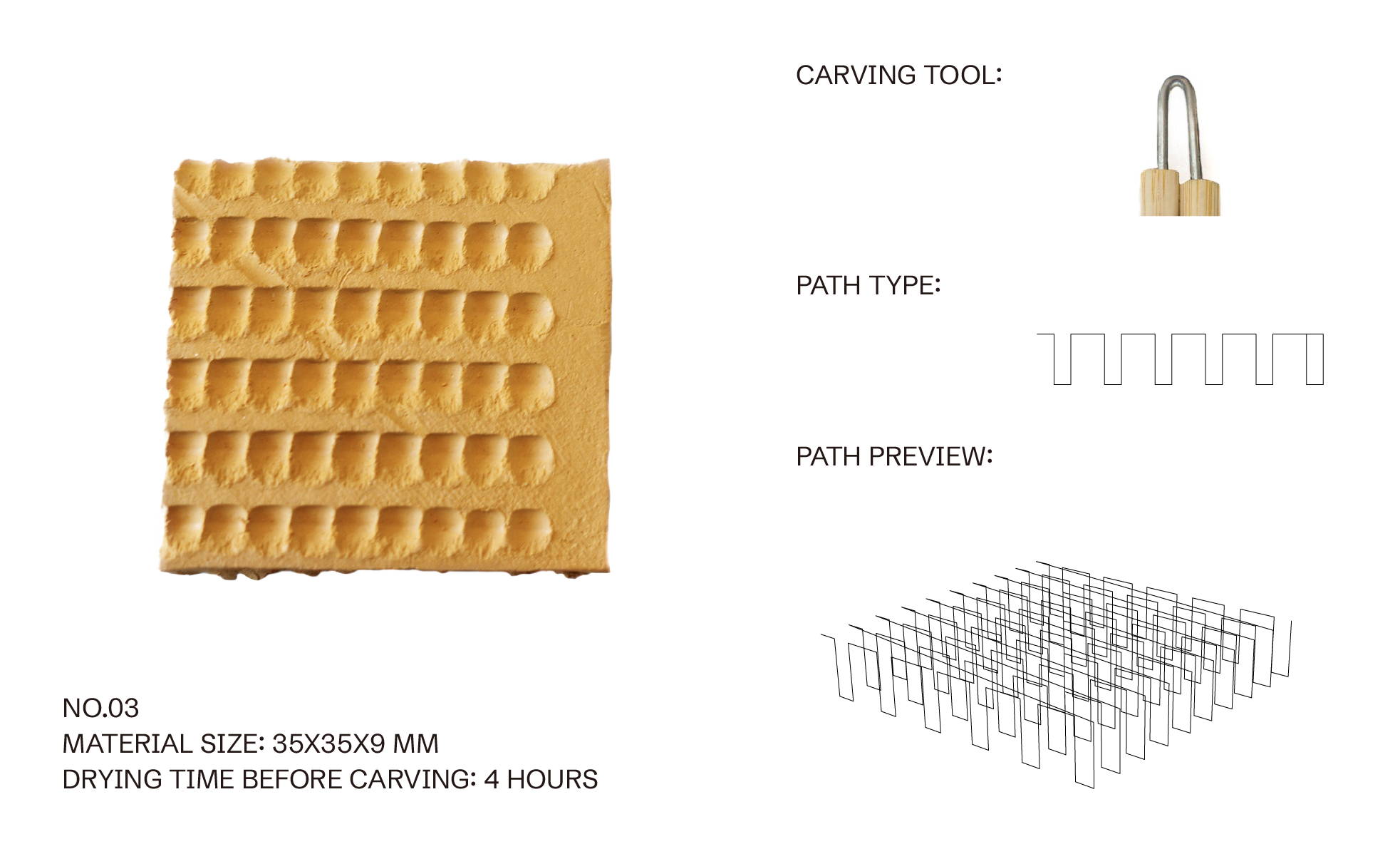

b. Full-dry Clay with CNC Milling:
Fully dried clay, being brittle, requires higher driller speeds and lower movement speeds for CNC milling. This study modified the DIY Pen Toolhead and adapted Ahmeted’s Ender 3 engraving method to create a Zmorph-compatible milling module.
Fully dried clay, being brittle, requires higher driller speeds and lower movement speeds for CNC milling. This study modified the DIY Pen Toolhead and adapted Ahmeted’s Ender 3 engraving method to create a Zmorph-compatible milling module.



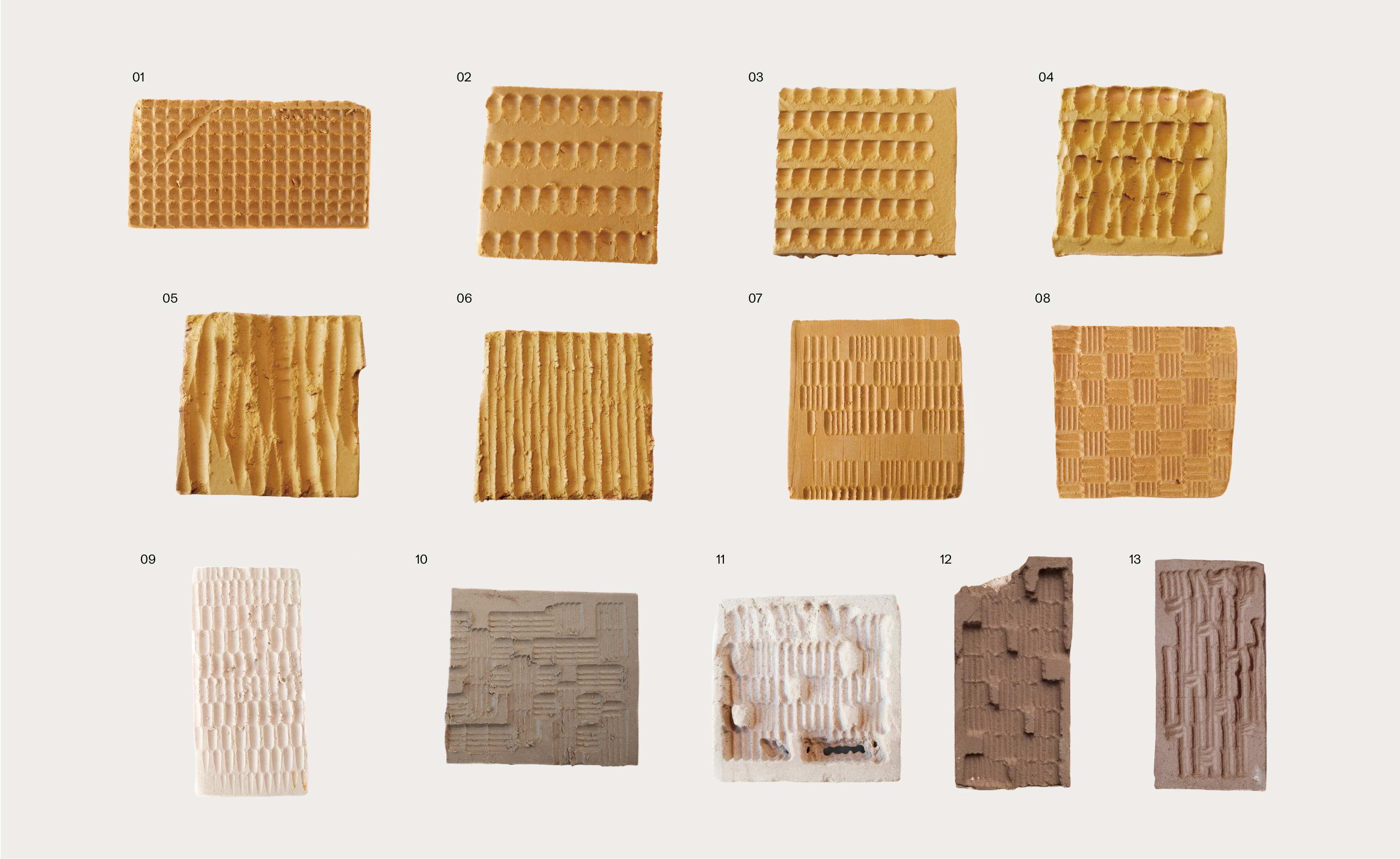
Firing
Microwave kilns offer a studio-friendly, low-cost, and energy-efficient alternative. Research by Peng et al. shows microwave kilns can fire small pieces in 24 minutes compared to 8 hours in traditional kilns, with a tenfold energy cost reduction, making them ideal for independent creators.
This study used a SHARP R-879 Microwave oven (26L, 900W) with a microwave kiln (Ø12.5 × H4 cm). Essential preparations include high-temperature gloves, a thermocouple thermometer (up to 1000°C), and insulating bricks or small clay pieces. Ensure the pieces are fully dry, with at least 3–4 days of indoor drying, to prevent explosions during heating.
During firing, keep the area around the microwave oven clear as the exterior becomes hot. Position the piece on 2–3 insulating bricks at the kiln’s center for even heat distribution, cover the kiln, and add fire bricks to the vent holes. Cycle through five power levels (90W to 900W) at 5 minutes per level, totaling 35 minutes. After heating, slightly open the kiln, insert a fire brick, and use the thermometer to measure the temperature. Bisque firing requires at least 800°C, though results may vary by clay type.
Allow the kiln to cool naturally for one hour before removing the piece. Avoid rapid cooling to prevent cracks in the piece or kiln coating. Let the kiln cool for a full day after firing to preserve the interior coating's lifespan.
Microwave kilns offer a studio-friendly, low-cost, and energy-efficient alternative. Research by Peng et al. shows microwave kilns can fire small pieces in 24 minutes compared to 8 hours in traditional kilns, with a tenfold energy cost reduction, making them ideal for independent creators.
This study used a SHARP R-879 Microwave oven (26L, 900W) with a microwave kiln (Ø12.5 × H4 cm). Essential preparations include high-temperature gloves, a thermocouple thermometer (up to 1000°C), and insulating bricks or small clay pieces. Ensure the pieces are fully dry, with at least 3–4 days of indoor drying, to prevent explosions during heating.
During firing, keep the area around the microwave oven clear as the exterior becomes hot. Position the piece on 2–3 insulating bricks at the kiln’s center for even heat distribution, cover the kiln, and add fire bricks to the vent holes. Cycle through five power levels (90W to 900W) at 5 minutes per level, totaling 35 minutes. After heating, slightly open the kiln, insert a fire brick, and use the thermometer to measure the temperature. Bisque firing requires at least 800°C, though results may vary by clay type.
Allow the kiln to cool naturally for one hour before removing the piece. Avoid rapid cooling to prevent cracks in the piece or kiln coating. Let the kiln cool for a full day after firing to preserve the interior coating's lifespan.


Year: 2024
Designer: Yaya Huang
Coach: Bahareh Barati @Eindhoven University of Technology @Sensory Matters Squad
Special thanks: Jian You Li 李建佑, Jia Lin Tsai 蔡佳霖 釉彩家