Aqua-Morph: A Design Method for Fabricating Shape-Changing Hydrogel Structures
Soft robotic actuators can create new uses and expressions for tangible and embodied interaction. Hydrogels, popular in soft robotics for their reversible shape-changing properties, often require technical expertise and specialized laboratories for fabrication, limiting rapid iteration. Additionally, aesthetic and form-giving qualities important to designers are often overlooked. We presents Aqua-Morph, an accessible design method for fabricating 3D-printed hydrogel-based structures that self-actuate in water.
Our contributions are twofold: (1) a DESIGN MANUAL outlining the fabrication pipeline using Fused Deposition Modeling (FDM) 3D printing with digitally adaptable parameters for creating flexible actuators, and (2) a TANGIBLE MOVEMENT LIBRARY of shape-changing hydrogel structures to empower designers, creative roboticists, material scientists and engineers in creating tangible interactions.
Year: 2023
Researcher: Jing Ya Huang, Hannah Eikens, Amy Winters, Miguel Bruns
Research at @Sensory Matters Squad @Eindhoven University of Technology
Soft robotic actuators can create new uses and expressions for tangible and embodied interaction. Hydrogels, popular in soft robotics for their reversible shape-changing properties, often require technical expertise and specialized laboratories for fabrication, limiting rapid iteration. Additionally, aesthetic and form-giving qualities important to designers are often overlooked. We presents Aqua-Morph, an accessible design method for fabricating 3D-printed hydrogel-based structures that self-actuate in water.
Our contributions are twofold: (1) a DESIGN MANUAL outlining the fabrication pipeline using Fused Deposition Modeling (FDM) 3D printing with digitally adaptable parameters for creating flexible actuators, and (2) a TANGIBLE MOVEMENT LIBRARY of shape-changing hydrogel structures to empower designers, creative roboticists, material scientists and engineers in creating tangible interactions.
Year: 2023
Researcher: Jing Ya Huang, Hannah Eikens, Amy Winters, Miguel Bruns
Research at @Sensory Matters Squad @Eindhoven University of Technology
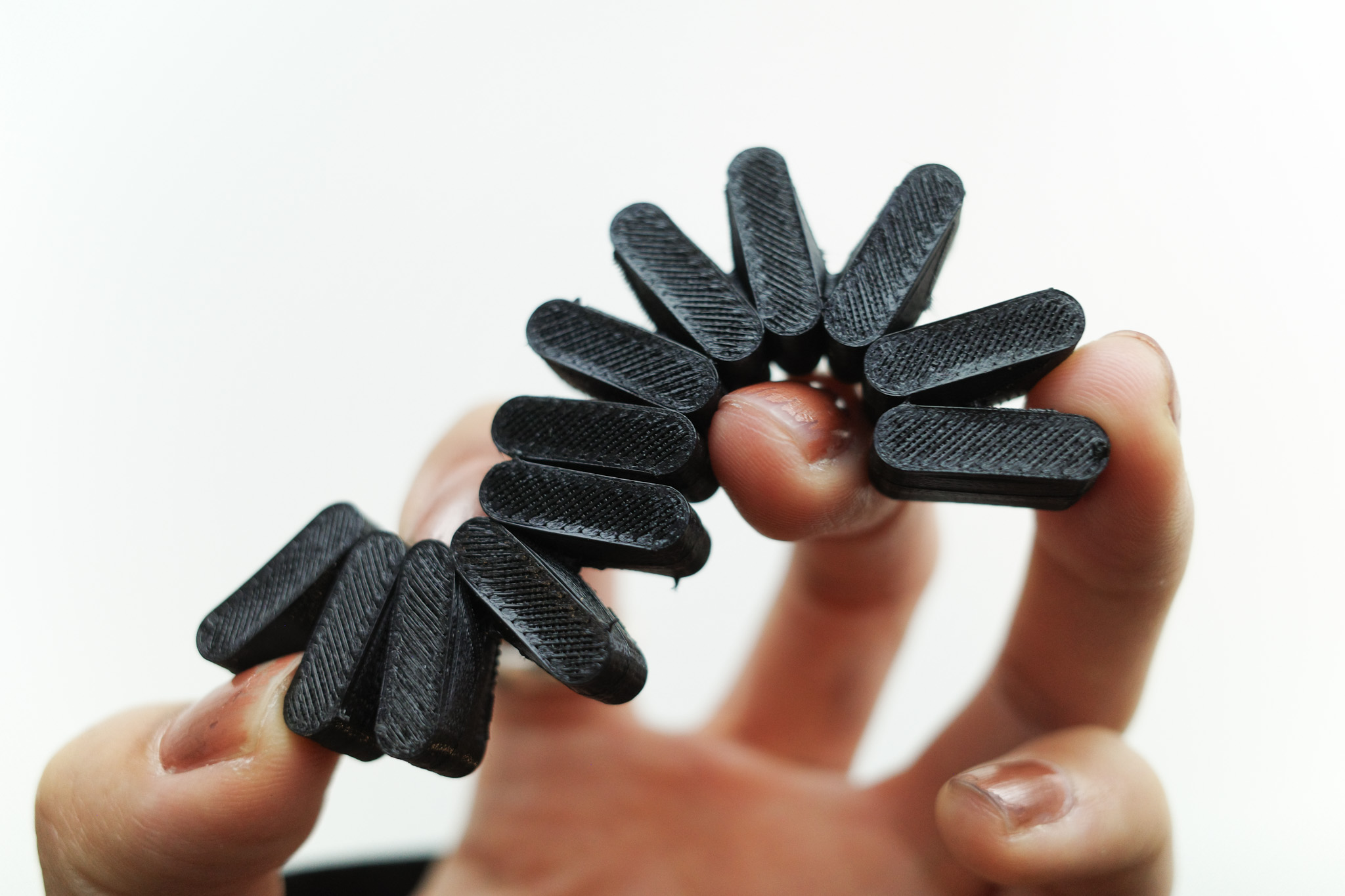
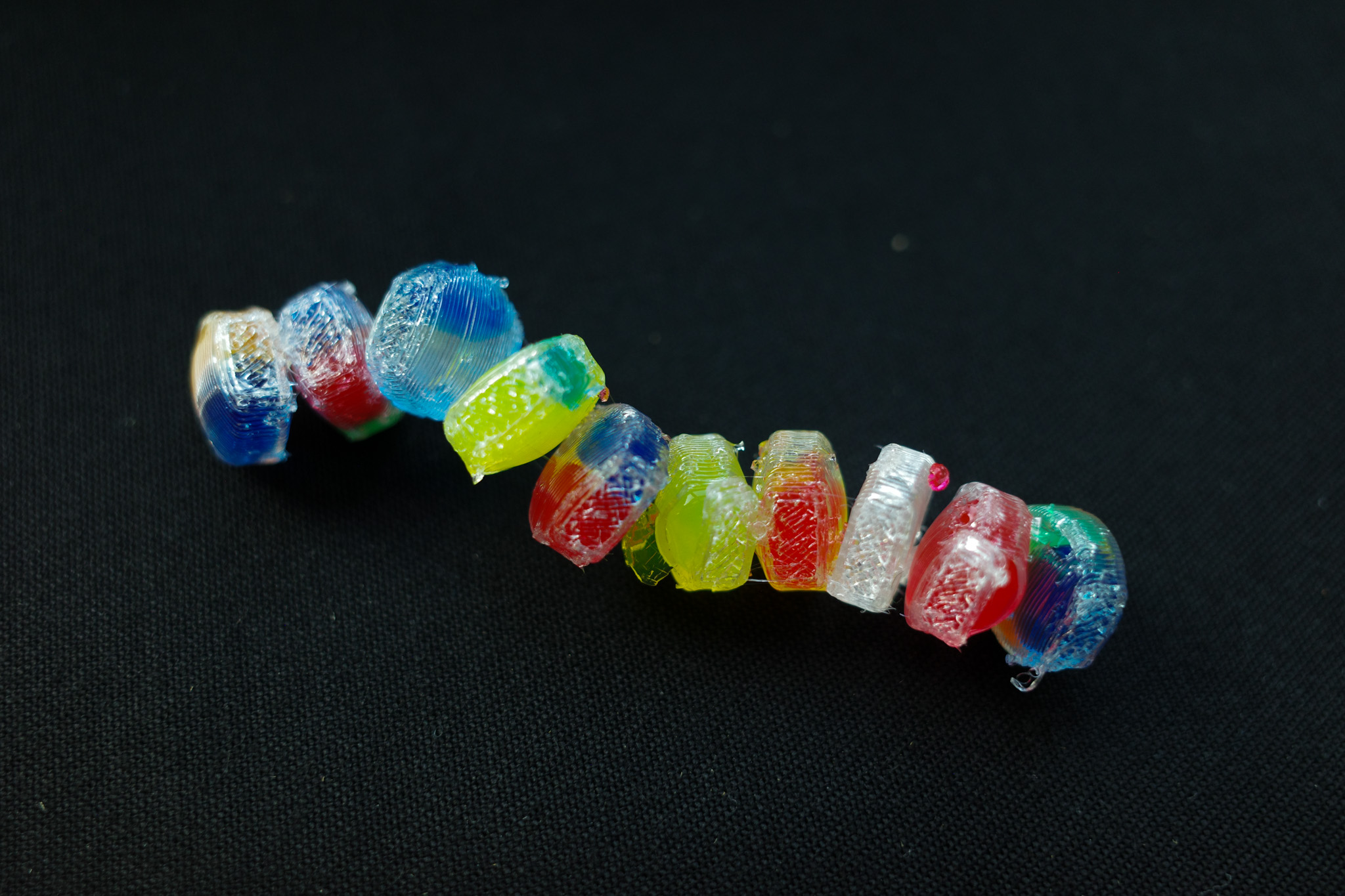
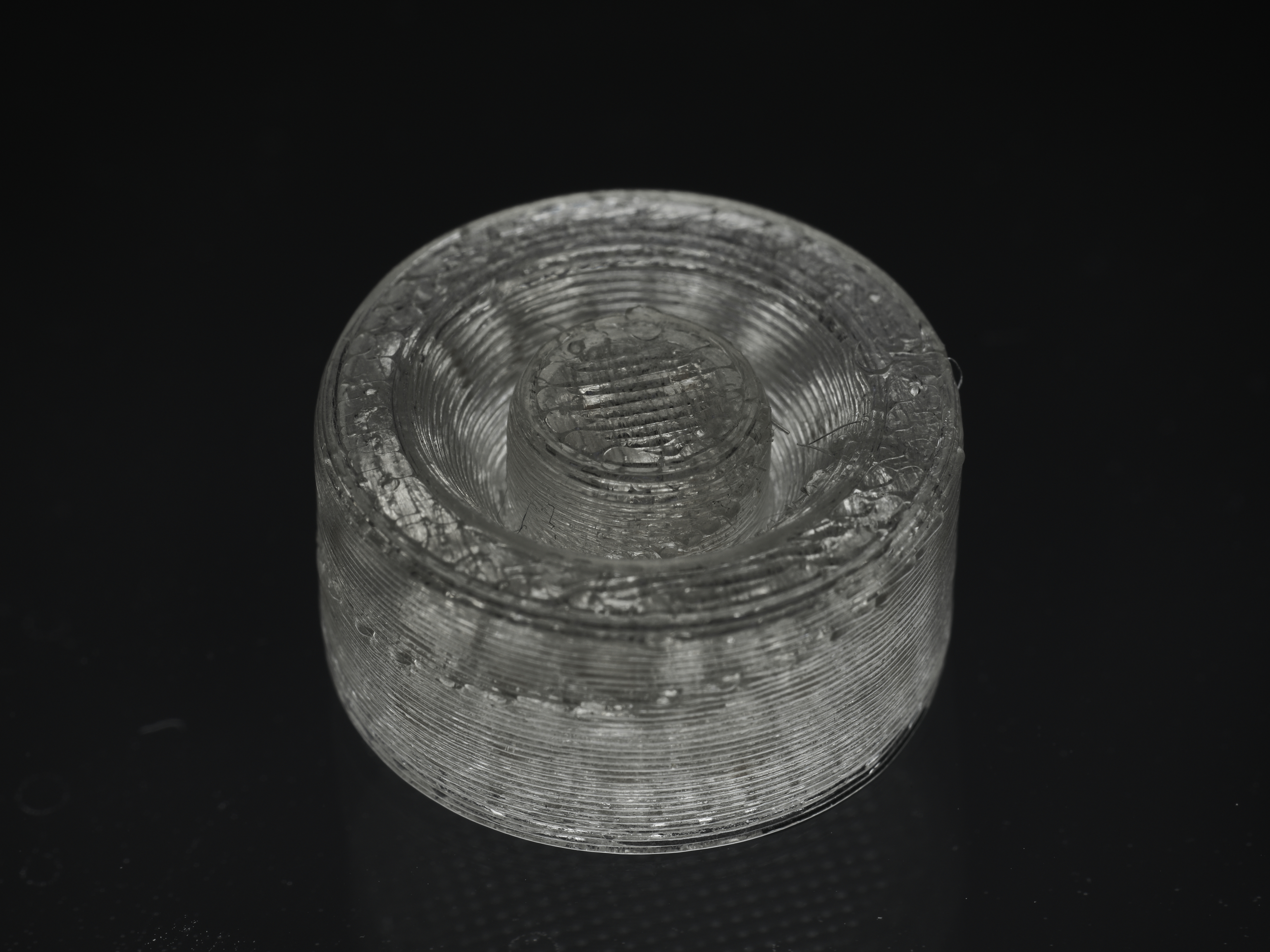
︎︎︎TEXTURE EXPERIMENT
We use Sodium polyacrylate (SPA), commonly found in everyday products like instant snow (powder) and decorative plant displays (beads). We observed that SPA hydrogel beads swell reversibly by absorbing water through sodium ions in the polymer. As shown in picture, the bead diameter increased from 2 mm (1) to 10mm, five times their size after 3 hours in water (2). Although the beads are elastic, they are fractured under compression from a rigid structure (3) and dehydrate reversibly back to their original size within 60 minutes and a week by a dehydrator and room temperature respectively (4).
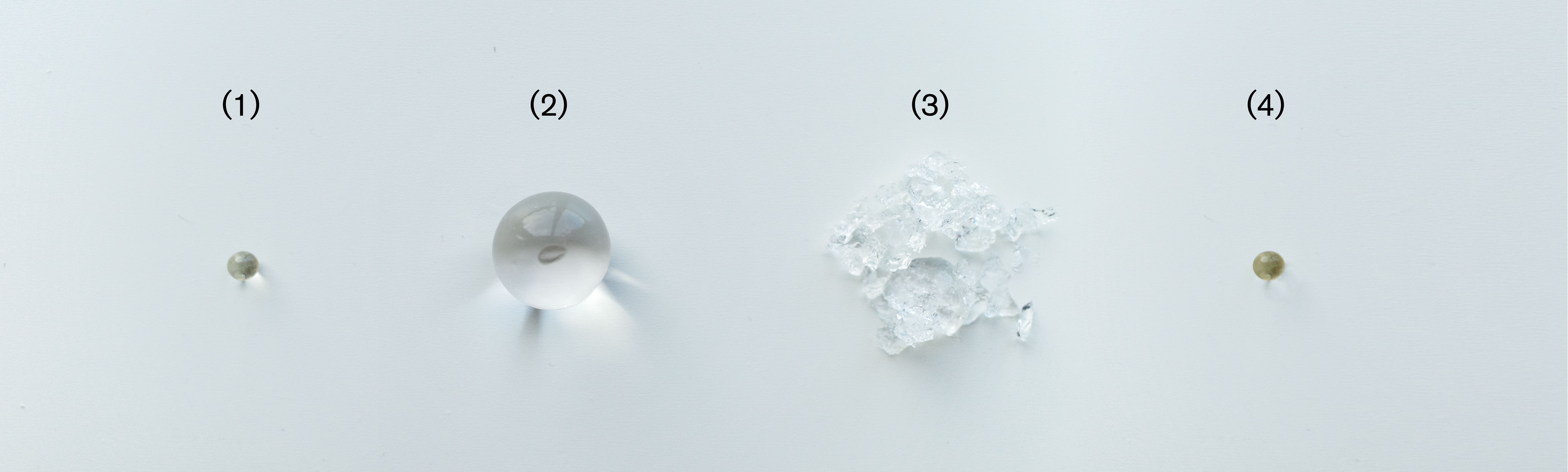
︎︎︎DESIGN MANUAL
The Design Manual offers a streamlined, easily replicable fabrication process using tools common in maker spaces. It requires a single FDM 3D printer and readily available materials like TPU filament and hydrogel beads. When placed in water, the beads expand, causing the printed object to bend, twist, and stretch.
Our design, manufacturing, and testing process consists of the following steps:
Step 1: Design and Slicing
Step
2: Printing
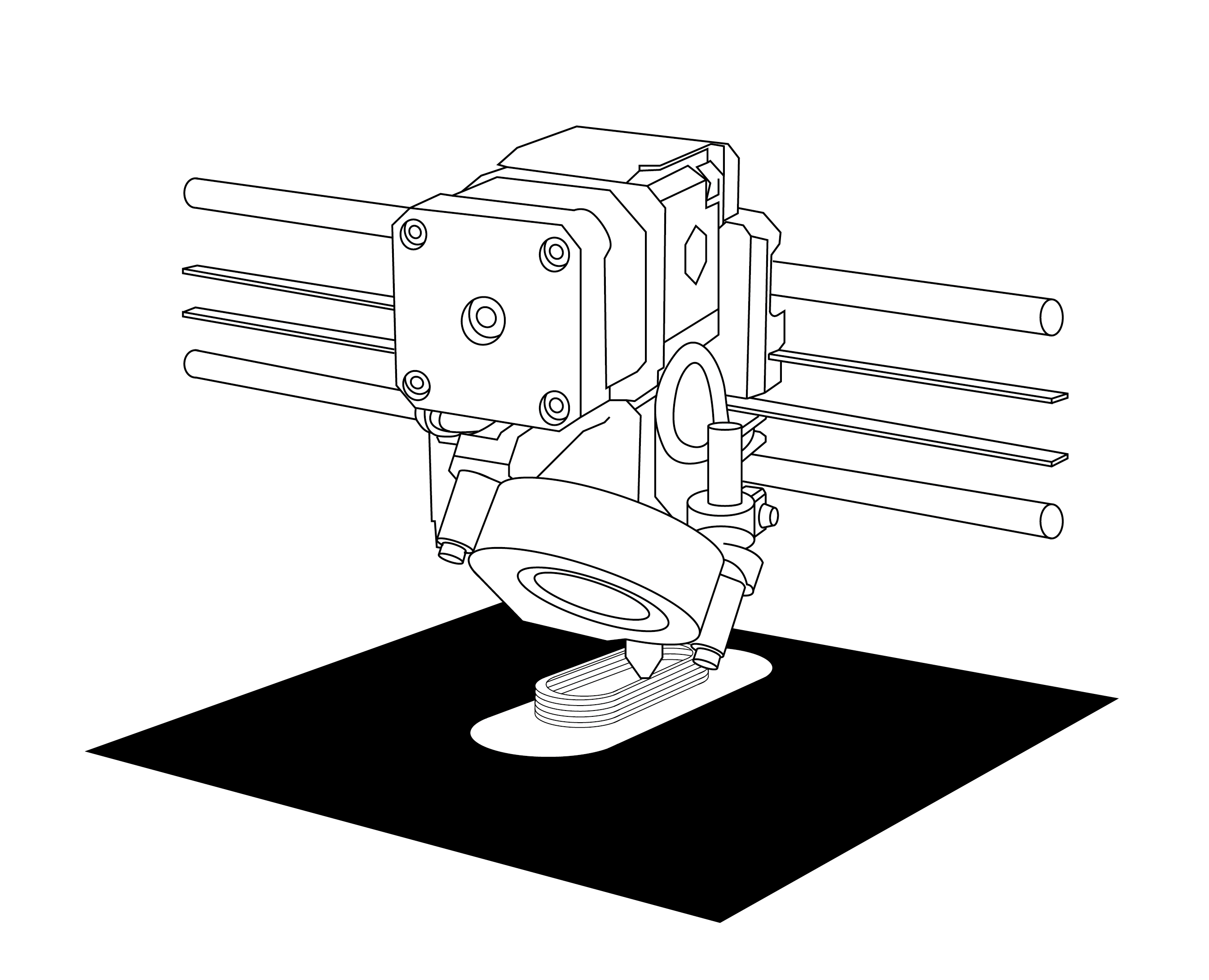
Step 3:
Pause the Printing
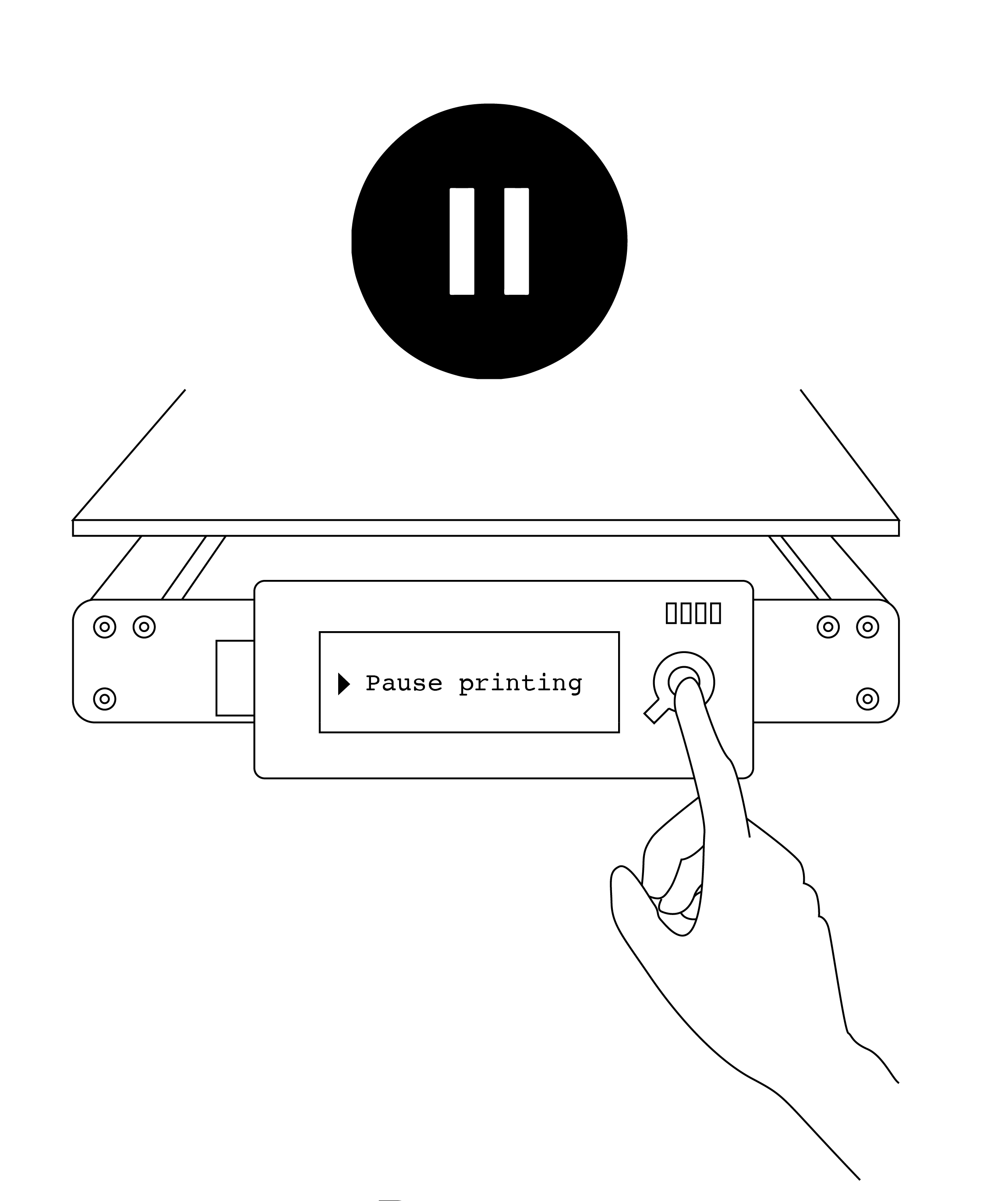
Step
4: Hydrogel Bead Integration
![]()
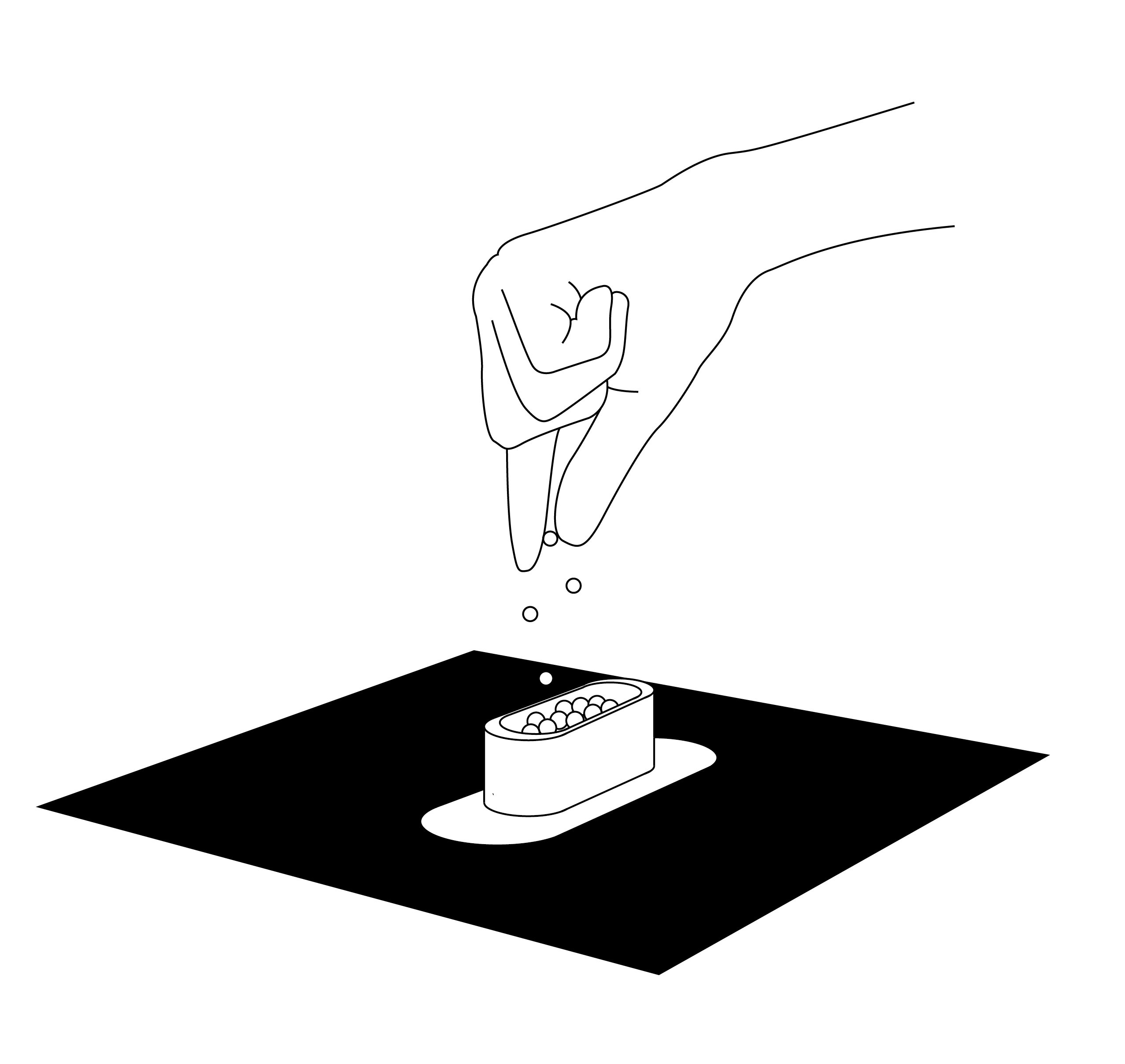
Step
5: Resume the Printing
![]()

Step
6: Actuation and Evaluation
![]()
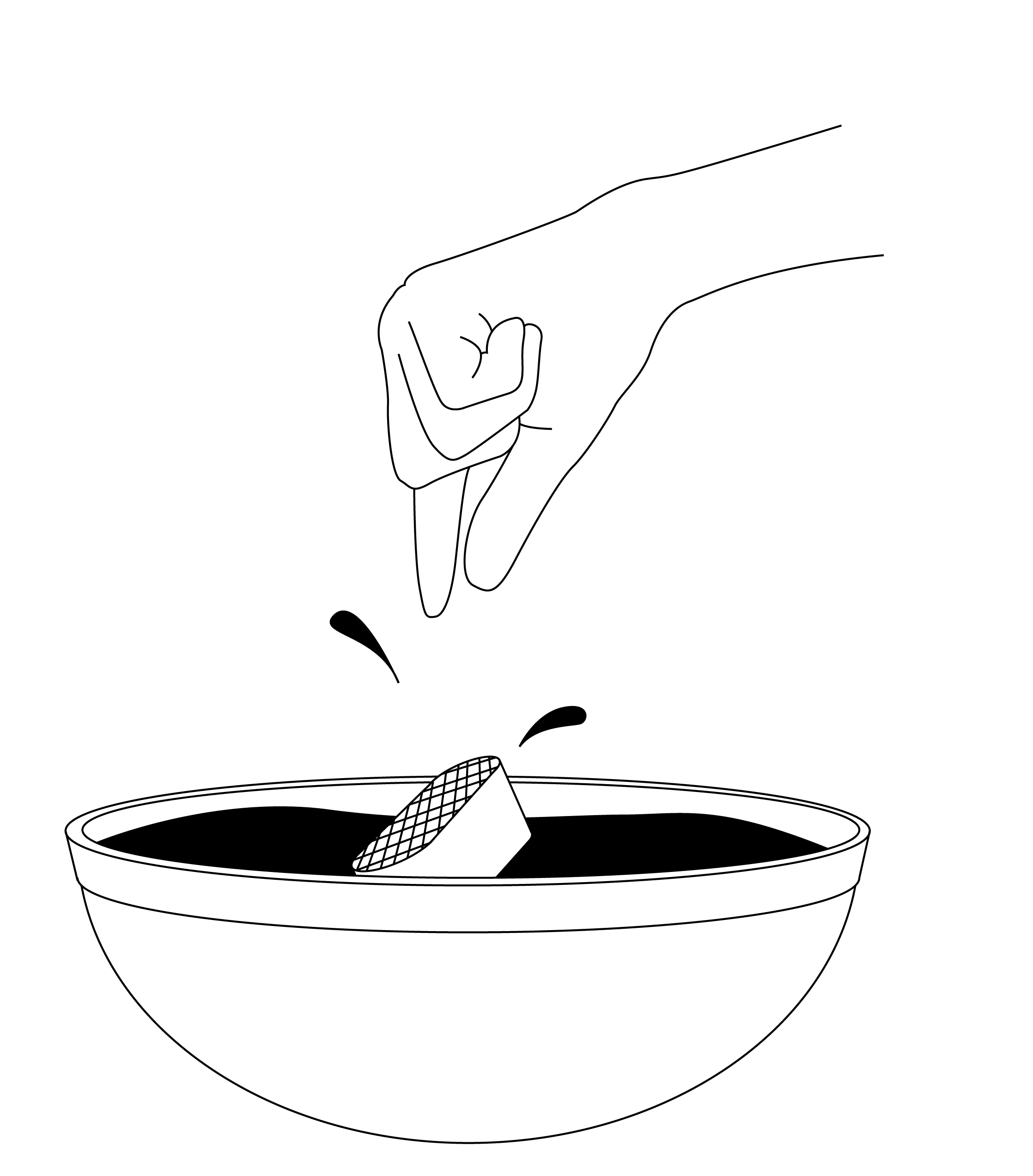
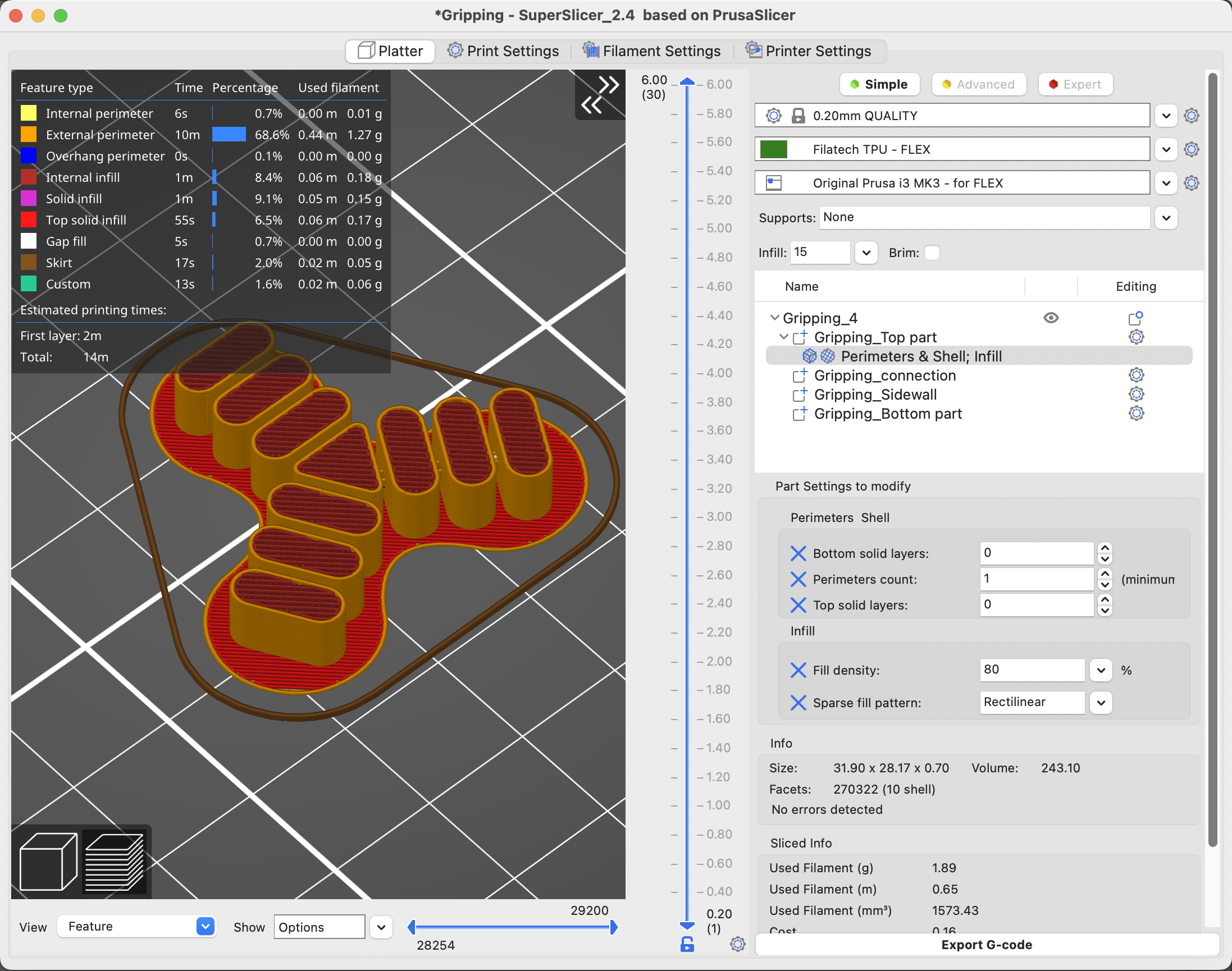
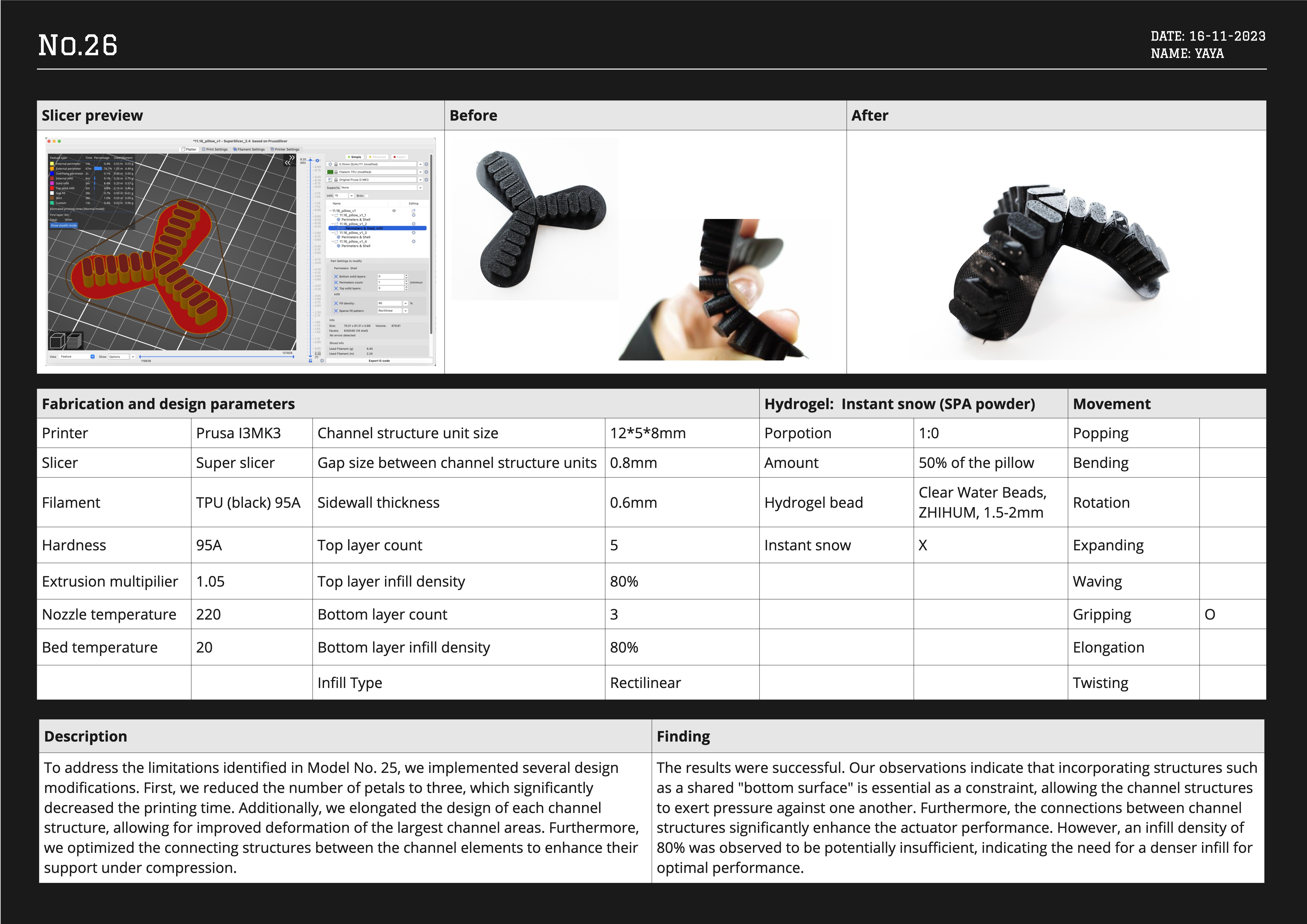
To
design hydrogel actuators, use CAD software to create the actuator shape with
an internal channel structure and seal it with a constraint layer. Model the
top and bottom channel layers separately and export as a 3mf file. Import these
into Super Slicer,
right-click to select "infill" and "perimeters shells," set
solid layers to zero, maintain one perimeter, and choose an 80-90% dense
rectilinear infill for a porous layer for liquid entry and hydrogel bead
encapsulation.
We recommend FDM 3D printers with standard nozzle sizes of 0.4 mm or 0.6 mm. Selecting the right filament is crucial for achieving the desired motion. An 85A hardness TPU filament is ideal due to its balance between flexibility and printability.
Super Slicer supports inserting a pause command into the g-code file. Use the layer overview slide bar, right-click to select “add pause print” ensuring the pause occurs before printing the top layer. At the designated pause, manually insert hydrogel beads into the actuator, ensuring careful placement and distribution within the channel structure. On completion, resume the printing with the specified infill pattern. Finally, submerge the actuator in water and record the actuation time on video. Record the findings in the diary after full actuation and classify the final movement.
We recommend FDM 3D printers with standard nozzle sizes of 0.4 mm or 0.6 mm. Selecting the right filament is crucial for achieving the desired motion. An 85A hardness TPU filament is ideal due to its balance between flexibility and printability.
Super Slicer supports inserting a pause command into the g-code file. Use the layer overview slide bar, right-click to select “add pause print” ensuring the pause occurs before printing the top layer. At the designated pause, manually insert hydrogel beads into the actuator, ensuring careful placement and distribution within the channel structure. On completion, resume the printing with the specified infill pattern. Finally, submerge the actuator in water and record the actuation time on video. Record the findings in the diary after full actuation and classify the final movement.
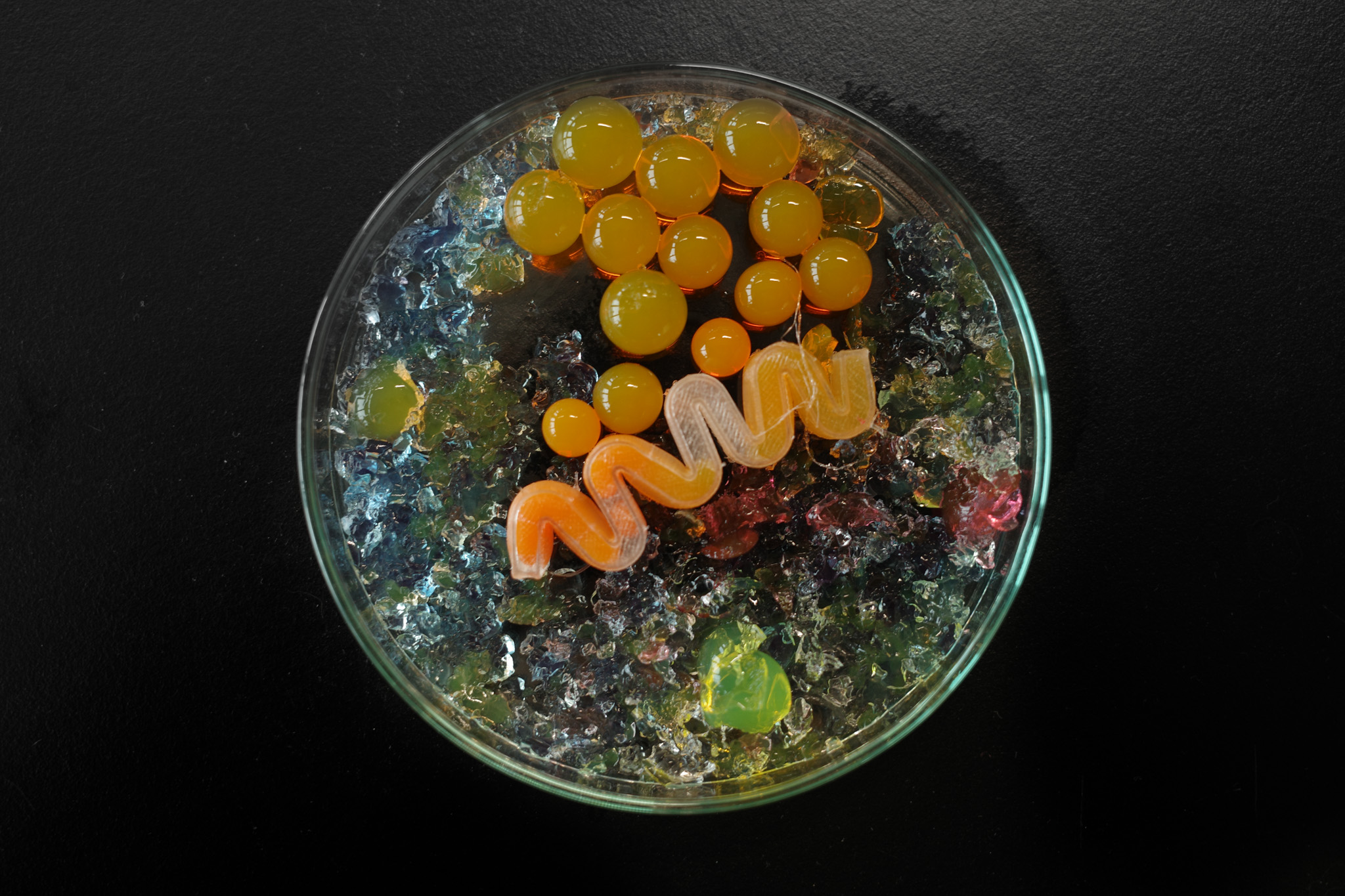
︎︎︎TANGIBLE MOVEMENT LIBRARY
The Tangible Movement Library showcases eight foundational movements: popping, expanding, elongating, bending, waving, twisting, rotating, and gripping. The movement performance of an actuator depends on the design of the channel structures that encapsulate the hydrogel. The choice and combination of connection and constraint plays a vital role in form variation. Our study identified several insights that contribute to the varying efficacy of different actuator designs:
(1) Connections between the structures enhance the actuator's performance.
(2) The shared surface can serve as a constraint for movements.
(3) The sidewall with the greatest surface area experiences the highest force, resulting in the most sizable extension.
(4) Larger actuators produce stronger movements.
(5) Designs may include multiple channels, where isolated hydrogel-filled sections exert pressure on each other.
The Tangible Movement Library showcases eight foundational movements: popping, expanding, elongating, bending, waving, twisting, rotating, and gripping. The movement performance of an actuator depends on the design of the channel structures that encapsulate the hydrogel. The choice and combination of connection and constraint plays a vital role in form variation. Our study identified several insights that contribute to the varying efficacy of different actuator designs:
(1) Connections between the structures enhance the actuator's performance.
(2) The shared surface can serve as a constraint for movements.
(3) The sidewall with the greatest surface area experiences the highest force, resulting in the most sizable extension.
(4) Larger actuators produce stronger movements.
(5) Designs may include multiple channels, where isolated hydrogel-filled sections exert pressure on each other.
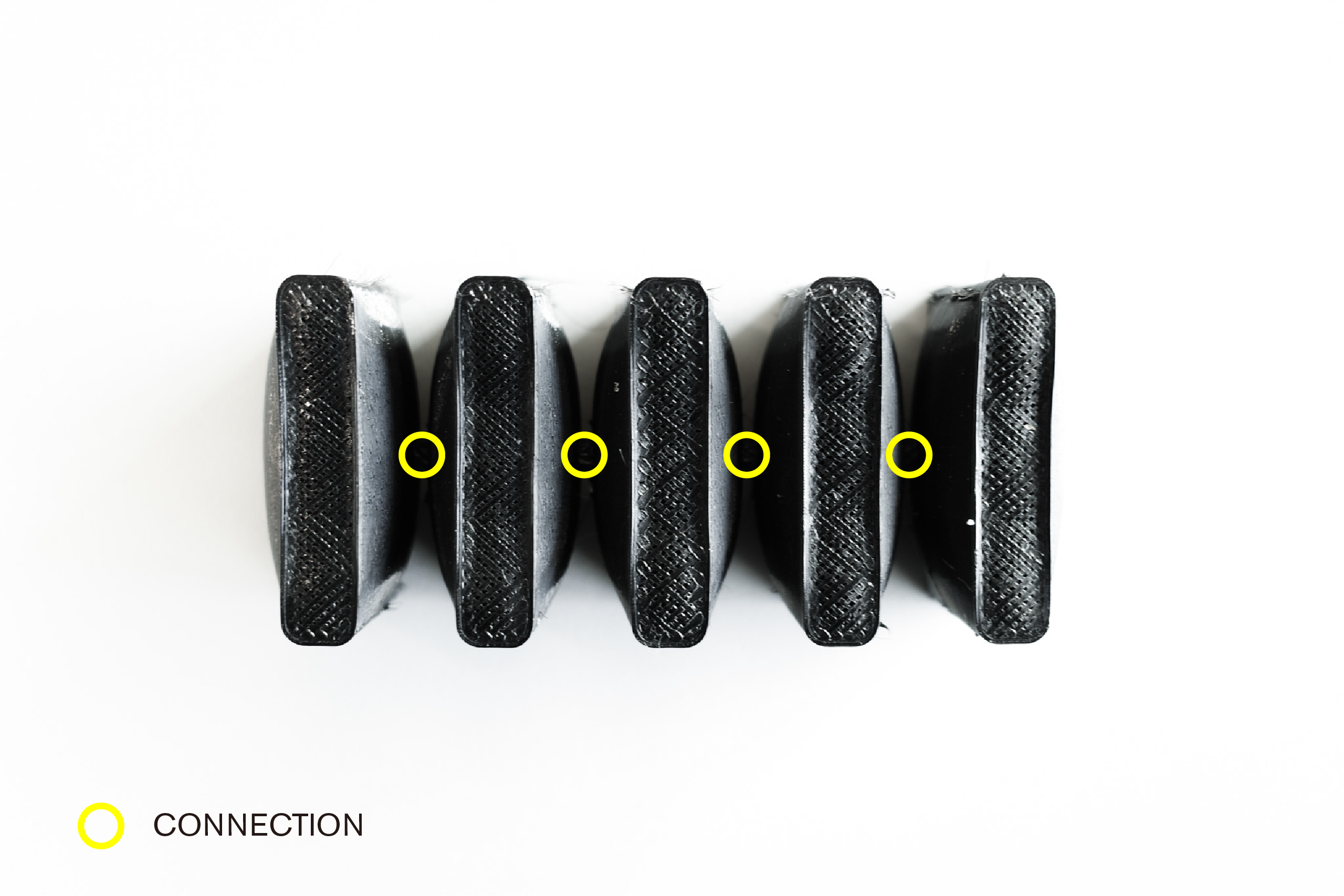
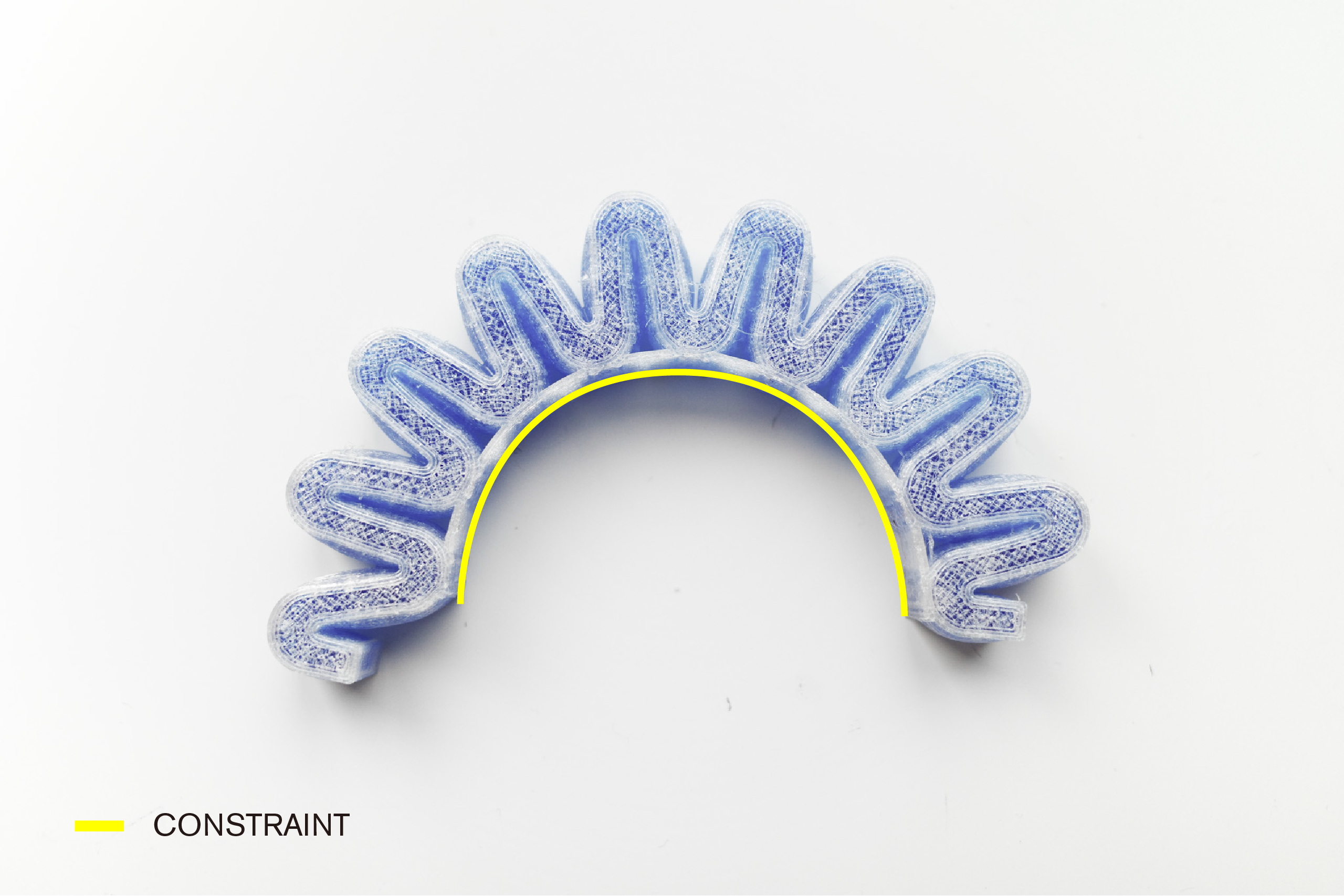
Gripping
![]()
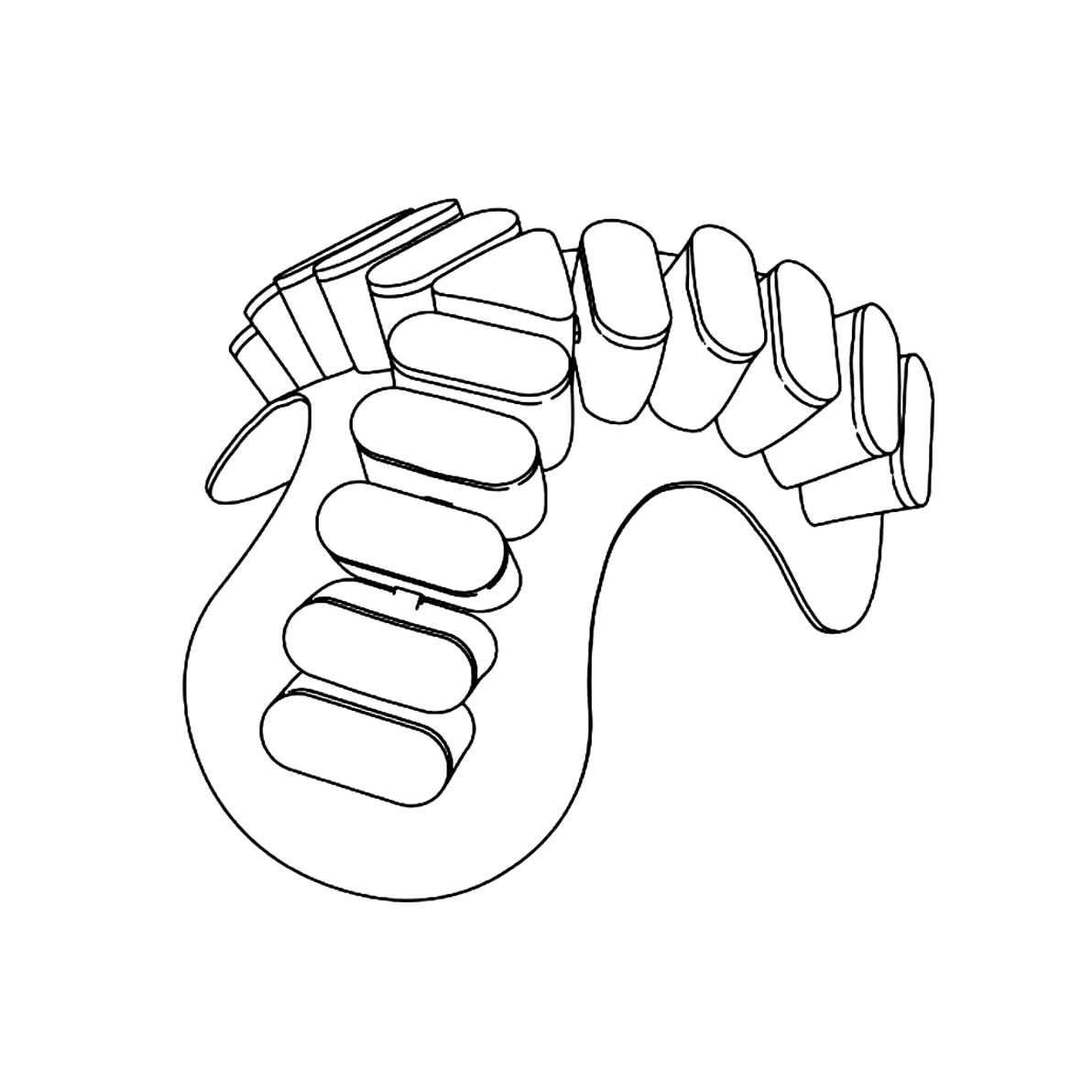
Expanding
![]()

Waving
![]()
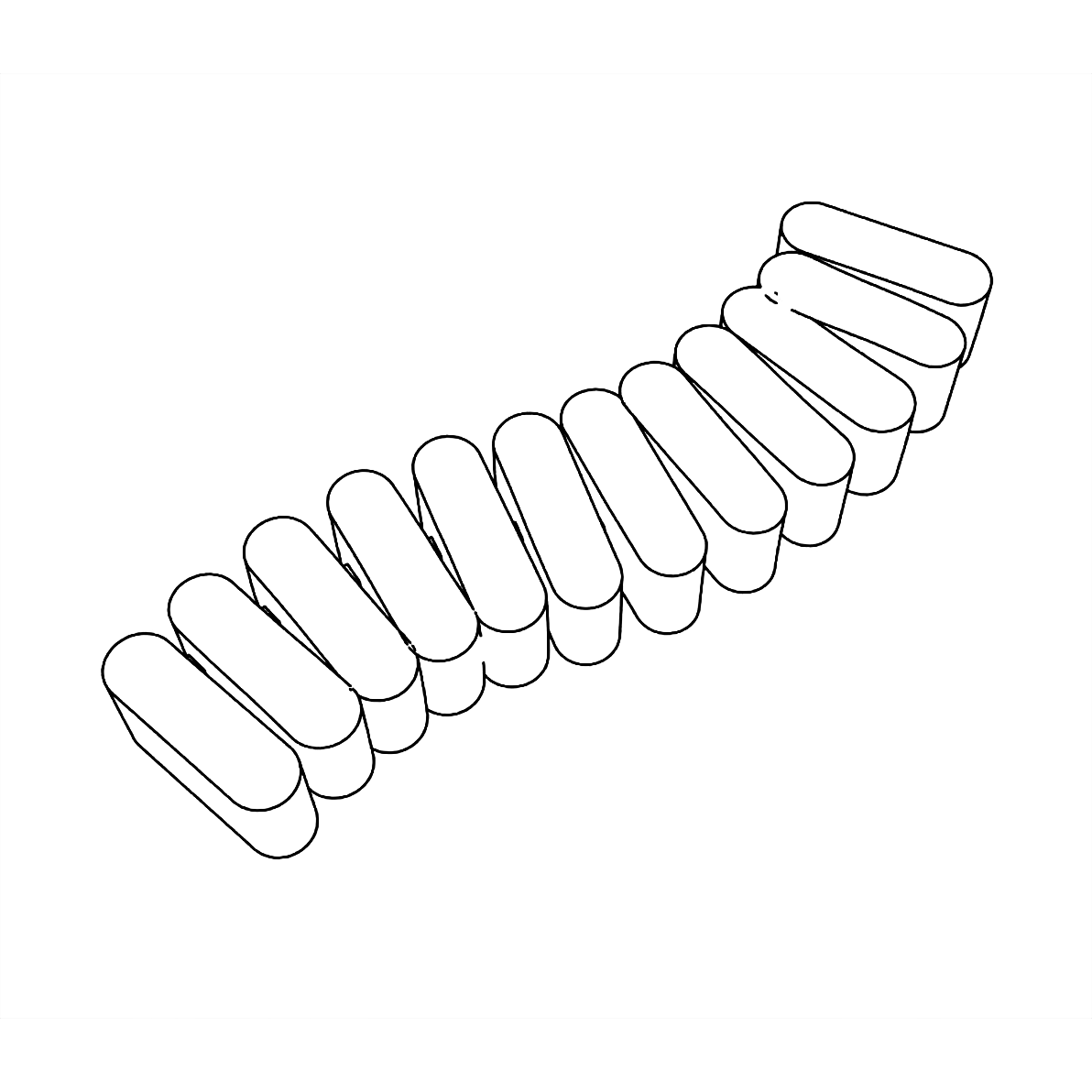
Twisting
![]()

Rotation
![]()
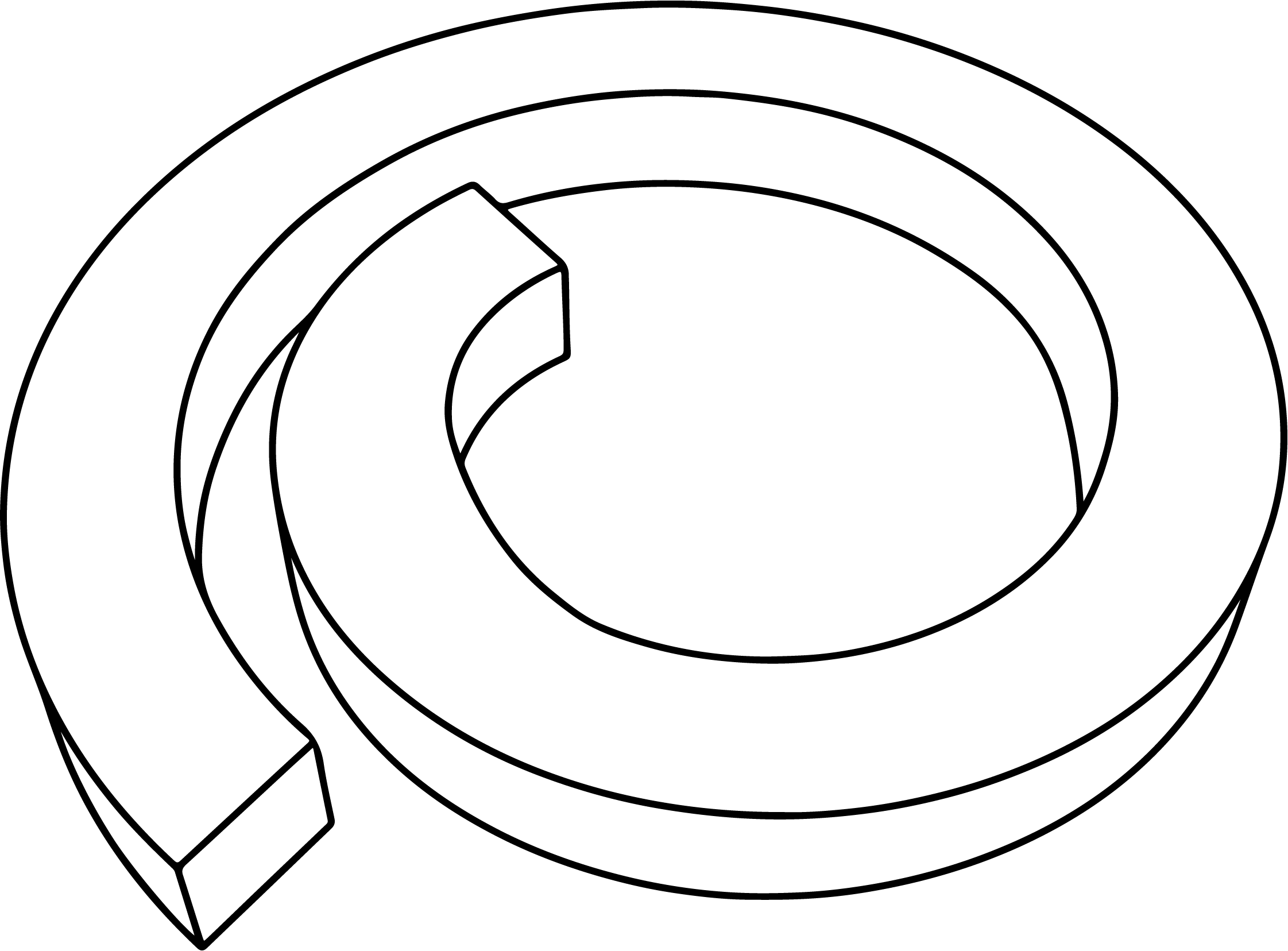
Popping
![]()
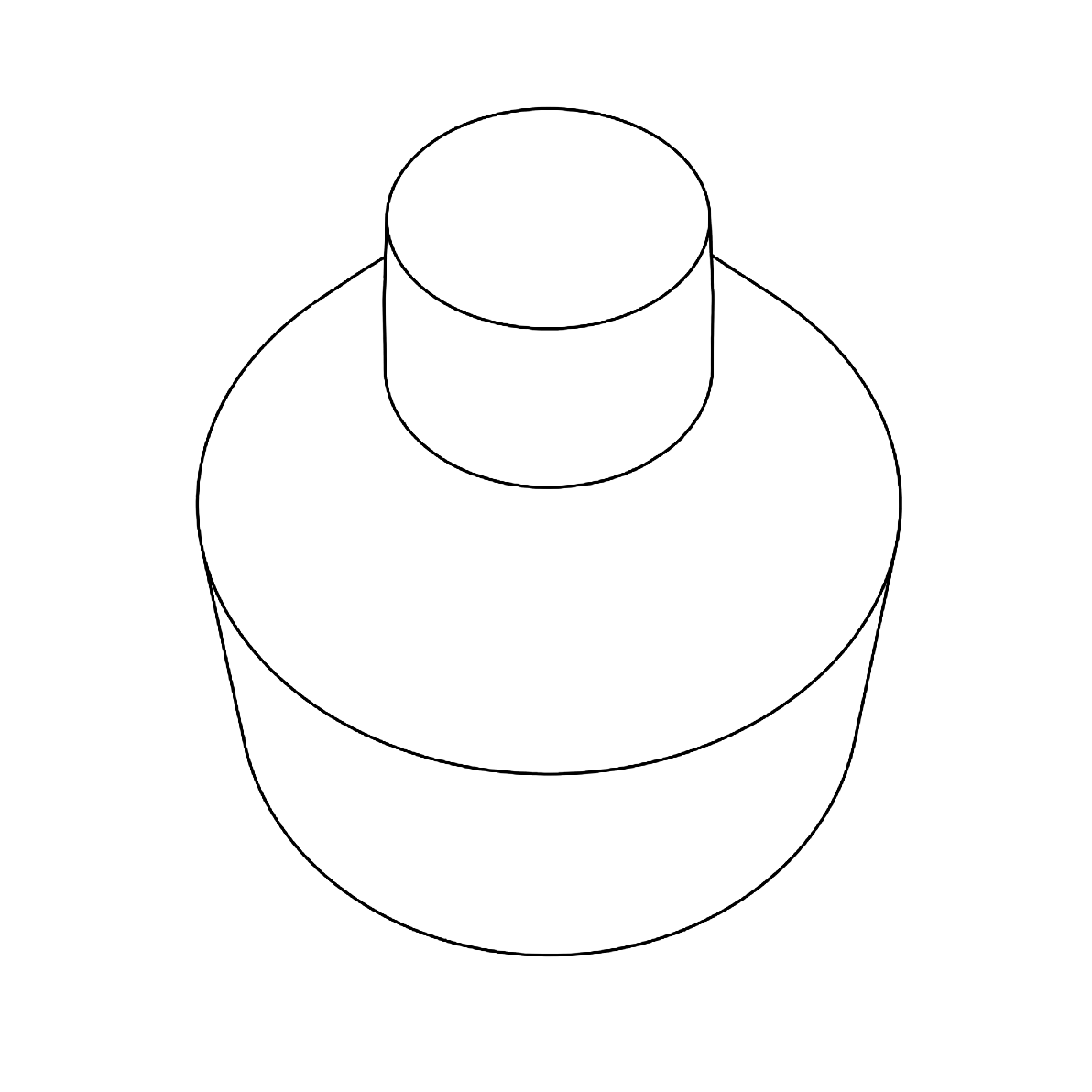
Bending
![]()
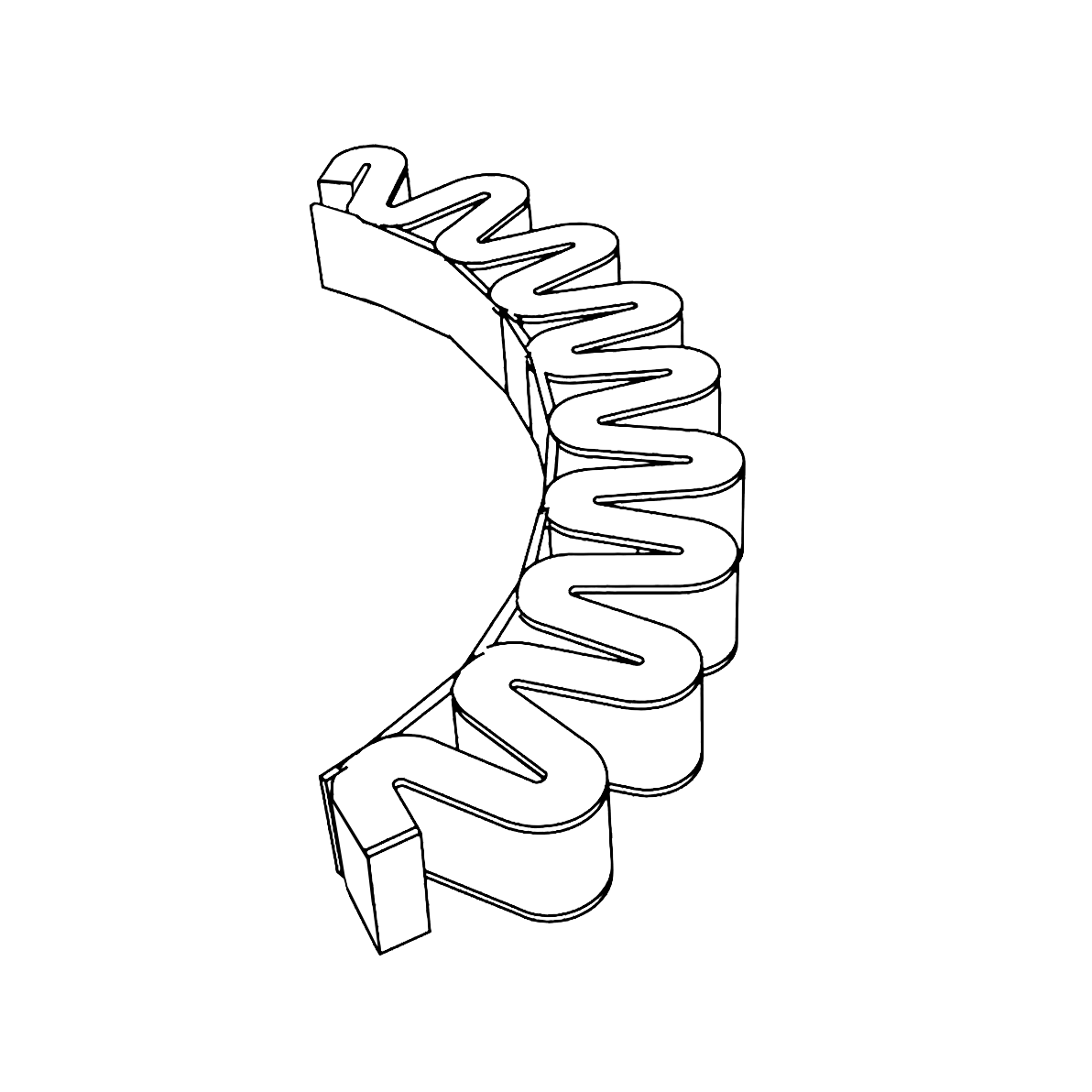
Elongation
![]()
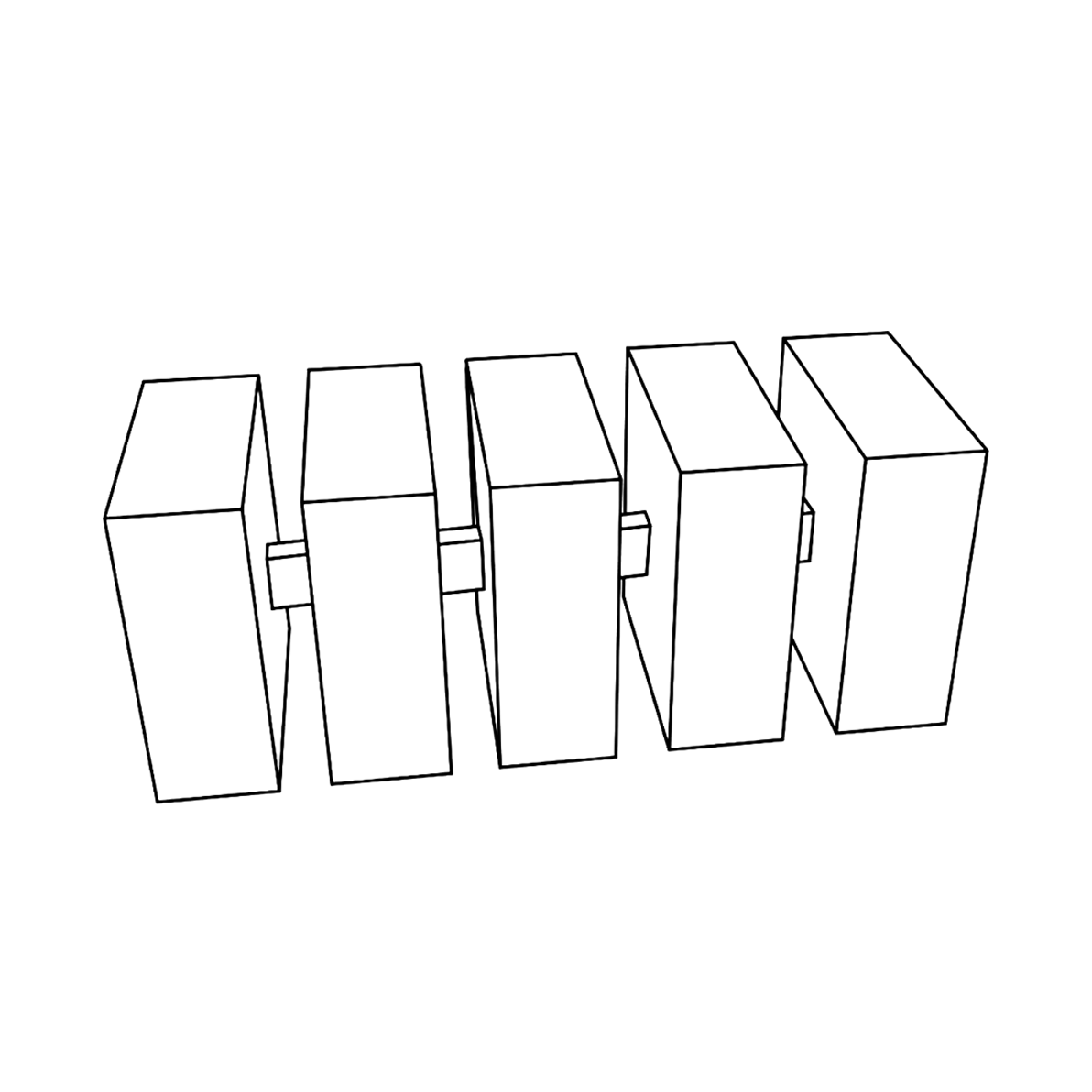
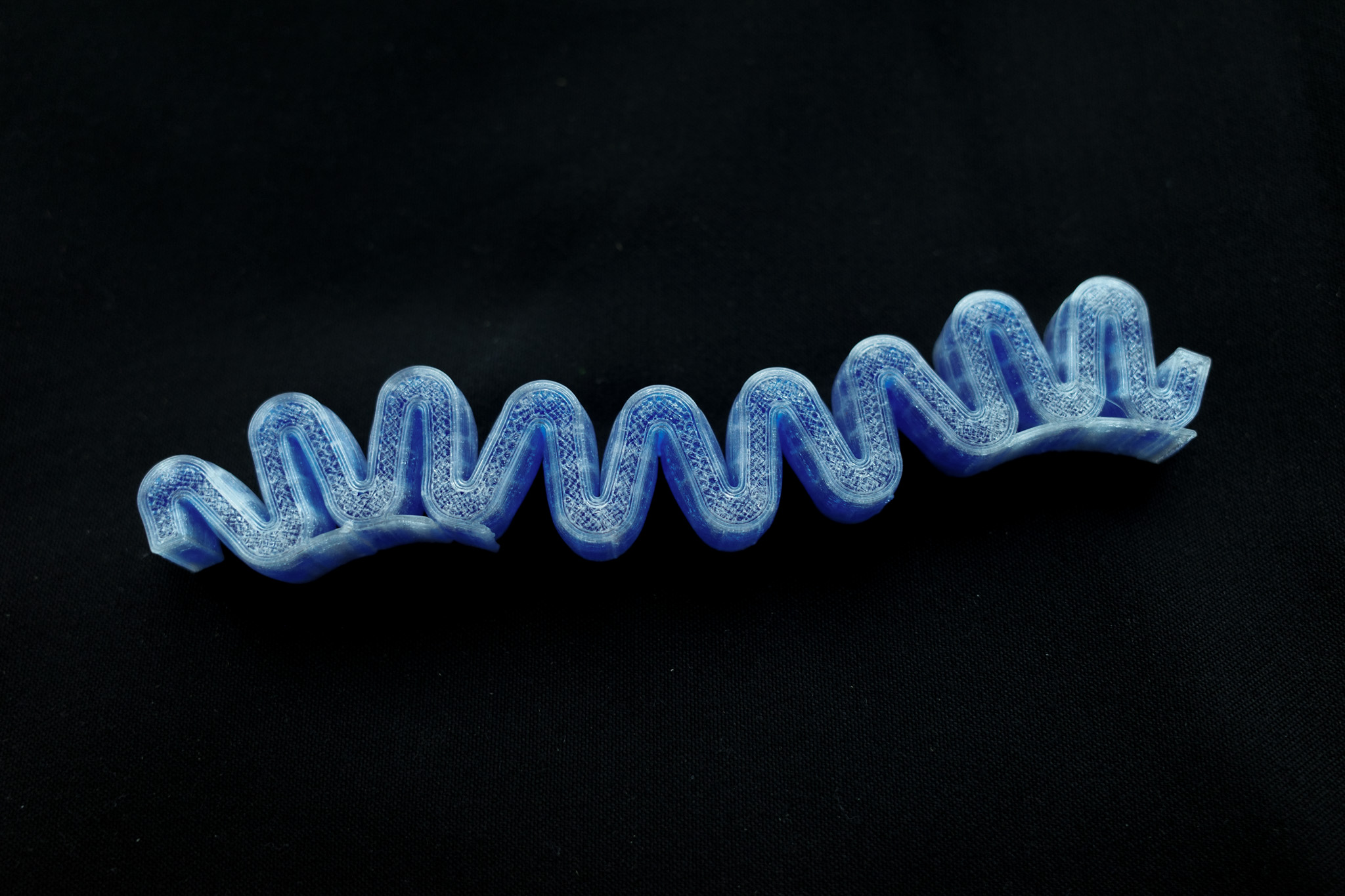
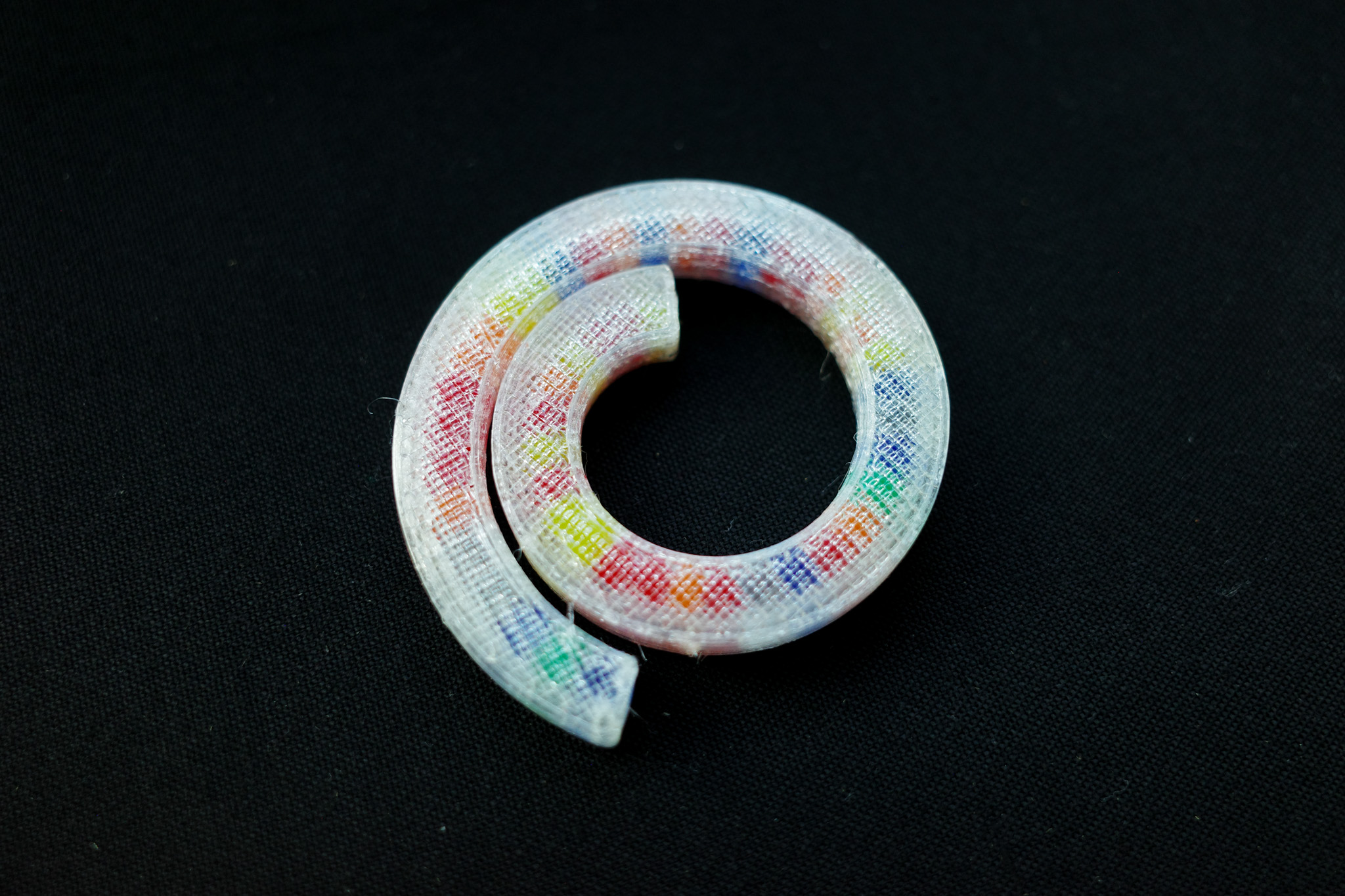
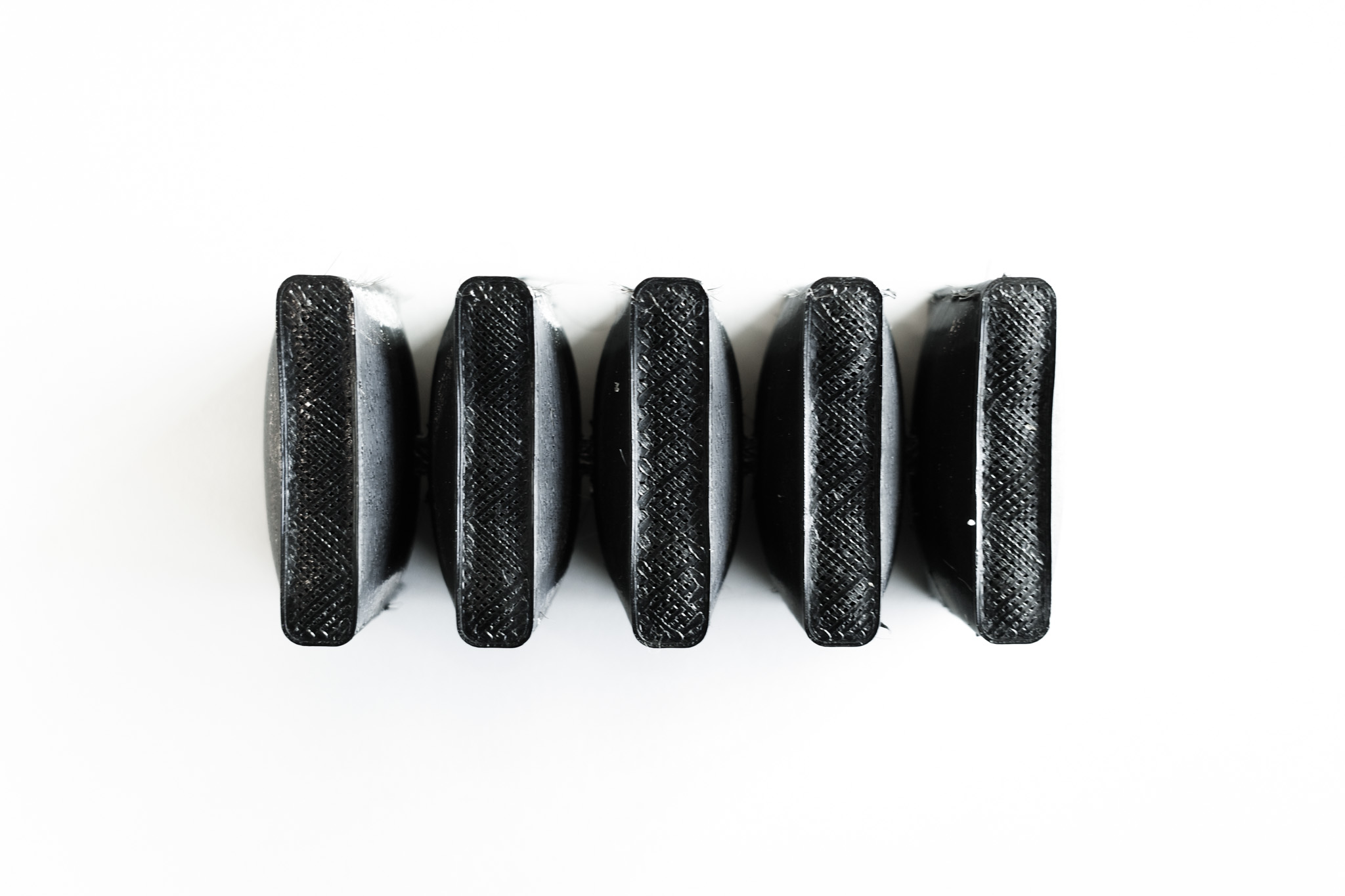
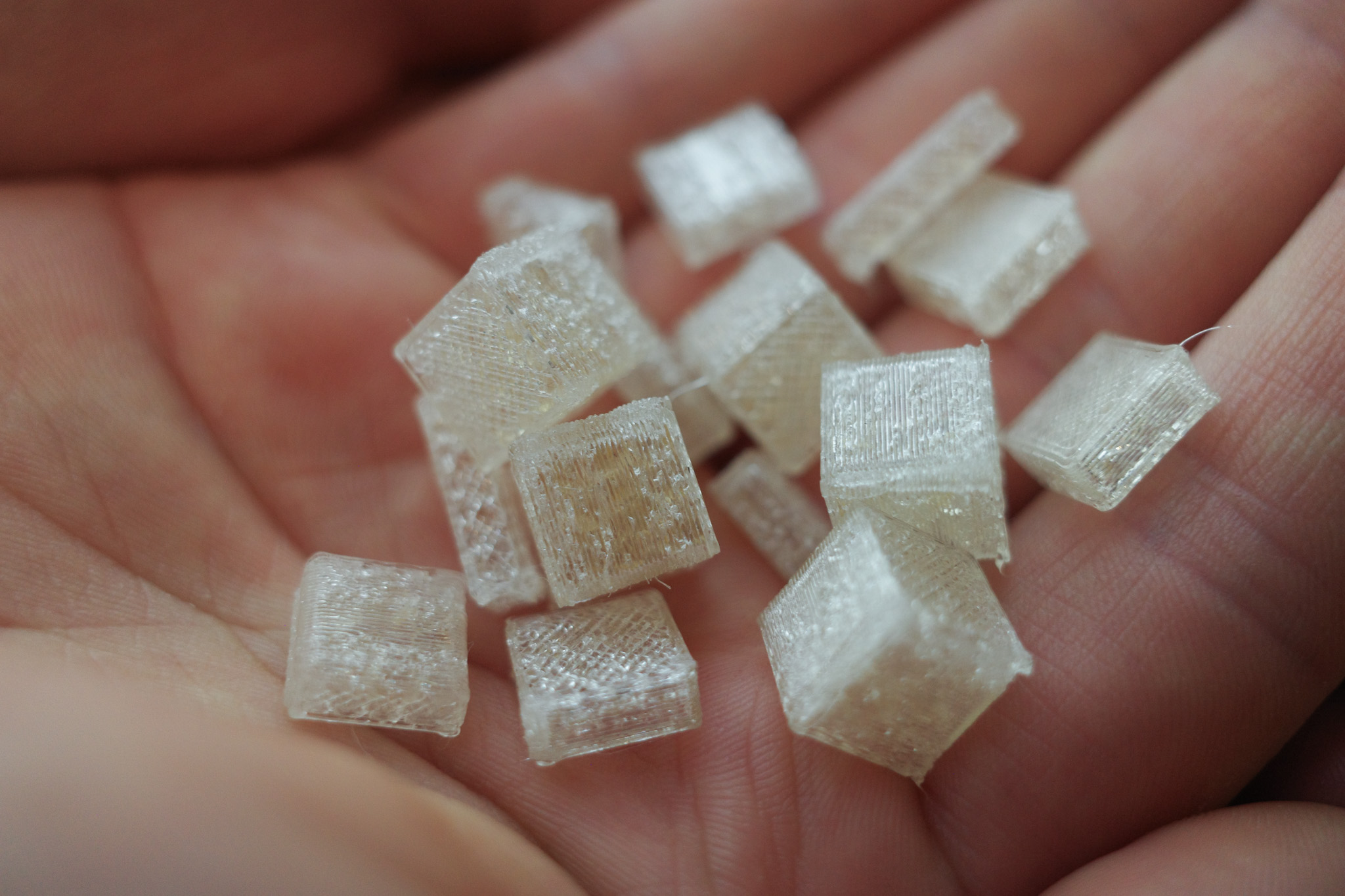
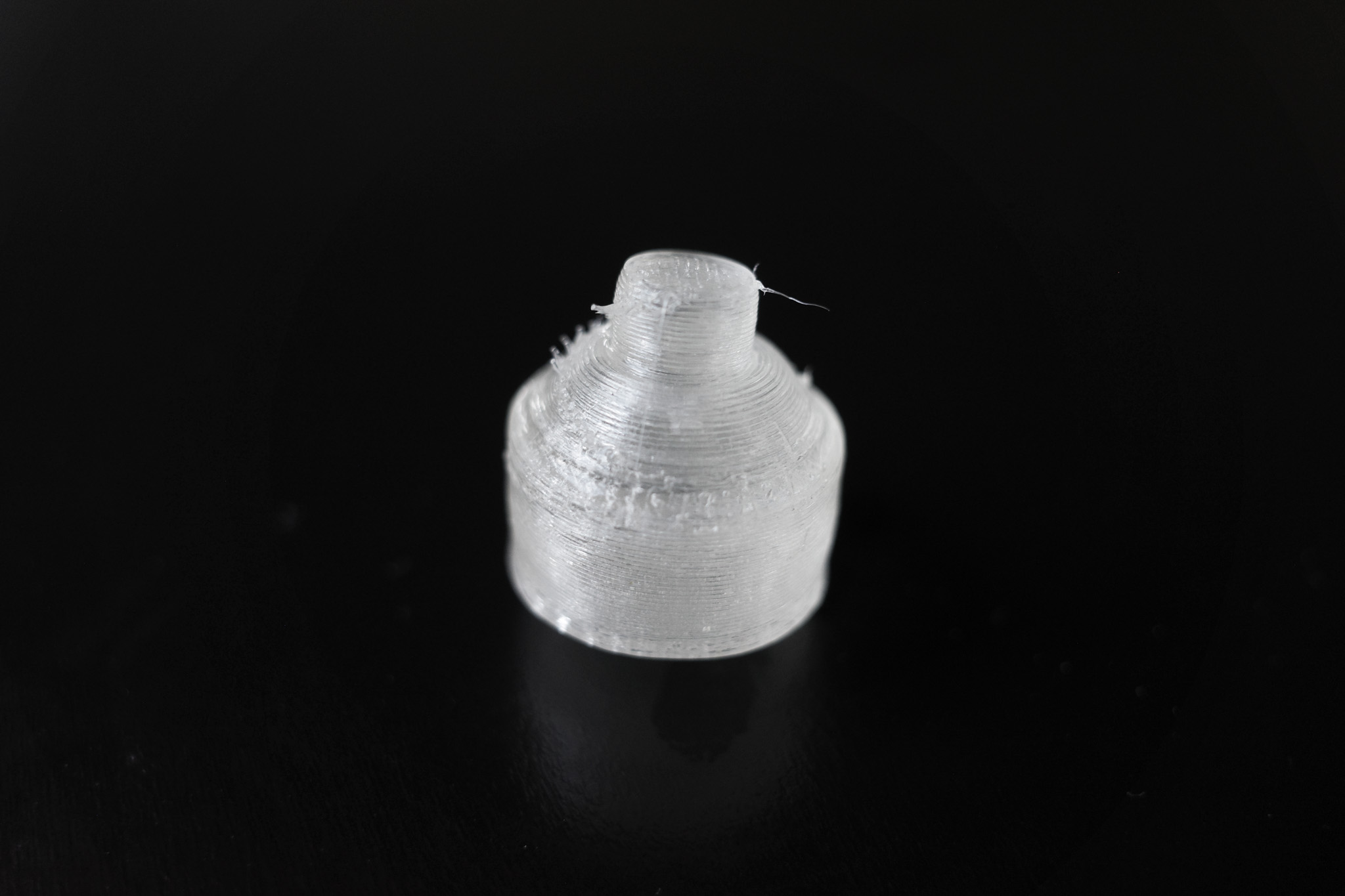
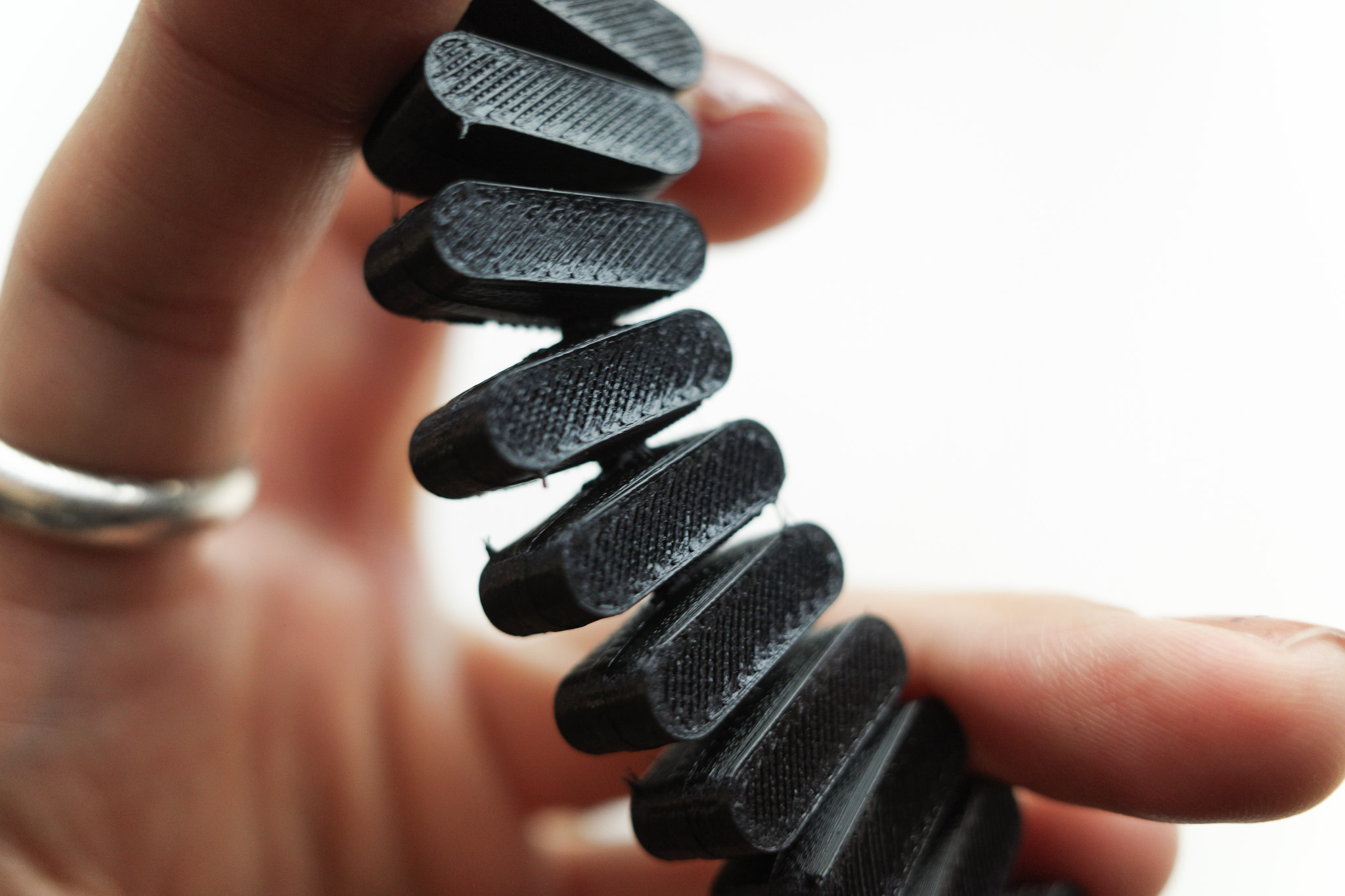
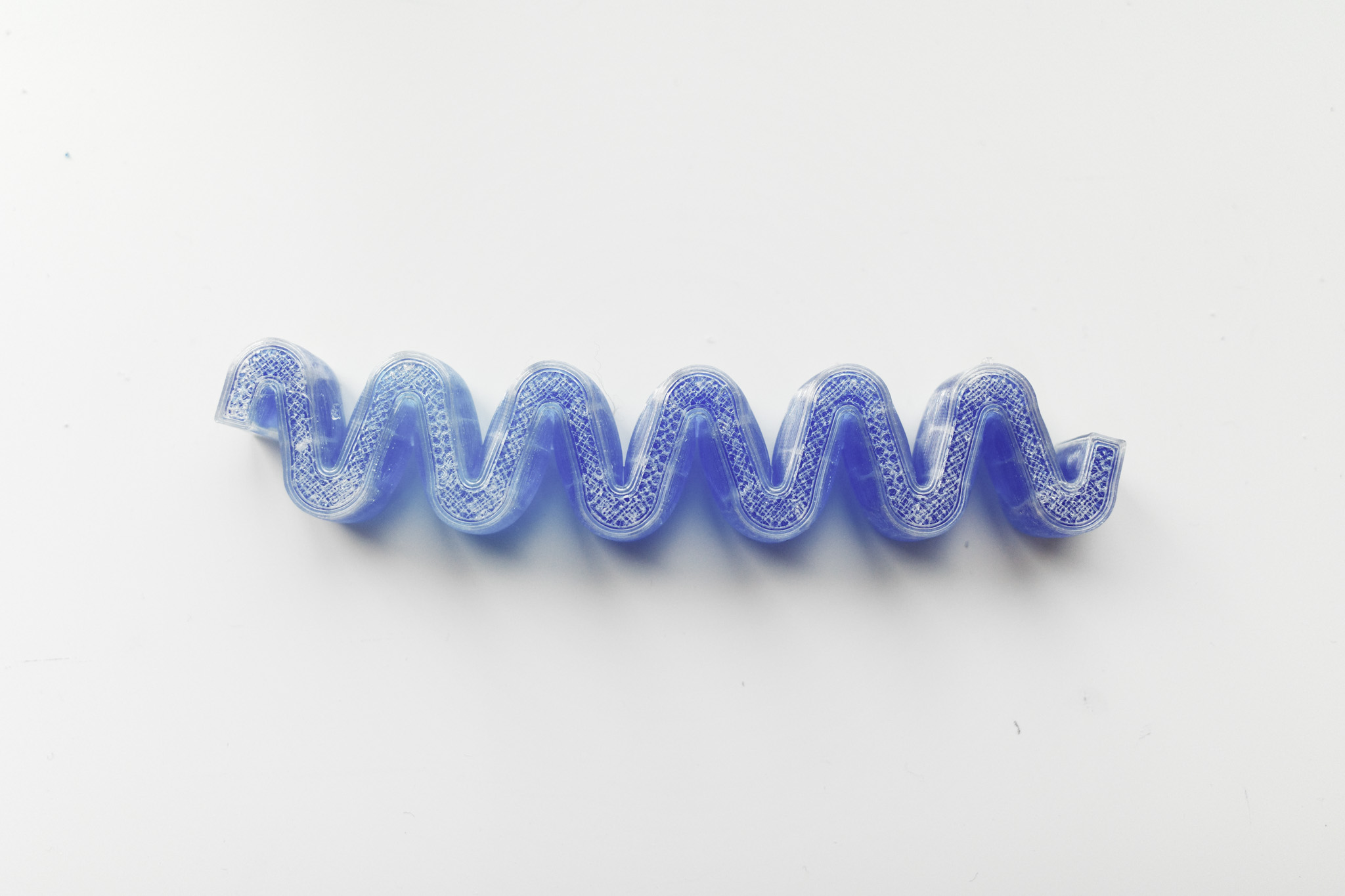
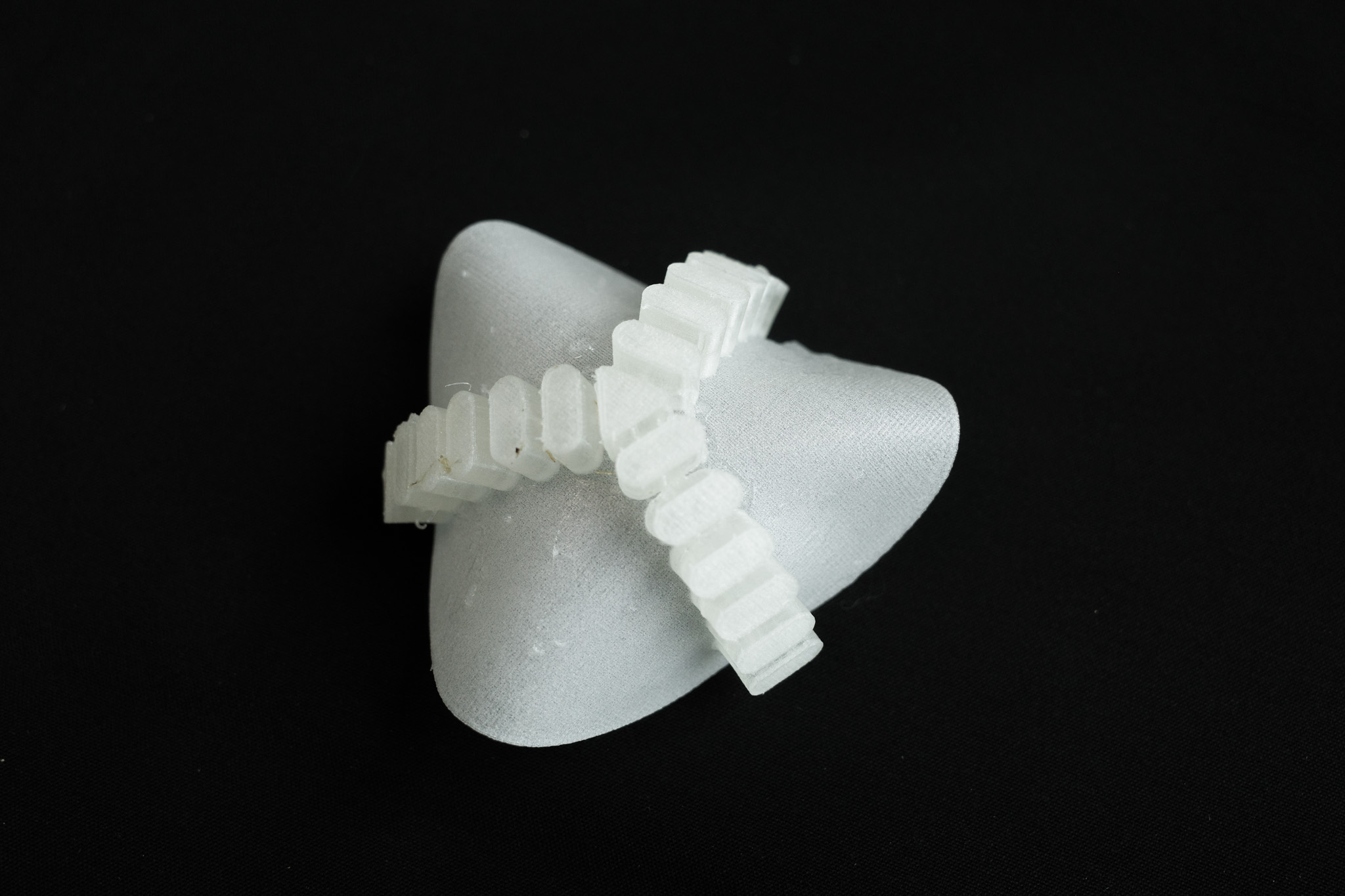
Our mixed-method Research through Design (RtD) and Material Driven Design (MDD) approach emphasizes systematic experimentation, incorporating diary templates for recording parameters and ensuring reproducible outcomes. Design Manual provides a step-by-step guide that empowers users with basic CAD and FDM printing skills to design, slice, and print actuators, democratizing the process and enabling customization.
By exploring both the fabrication challenges and the aesthetic sensibilities in soft robotics, our approach creates a more integrated and holistic design process for tangible and embodied interactions. Aqua-Morph's Tangible Movement Library, based on Brocker’s [1] actuator movement categories, values aesthetic perspectives and encourages free-form exploration.
Additionally, playfulness can bridge abstract concepts and their practical applications. Modular design serves as a free agency to encourage a playful learning experience , which facilitates the exploration of variations, enabling researchers to test different geometric configurations and observe their effects on movement.
This low-cost, accessible, and reproducible DIY approach uses readily available hydrogel beads. Aqua-Morph aims to enhance the Design-HCI soft actuator toolbox, inspiring researchers to explore modular configurations, aesthetics, and emerging responsive materials.
[1] Anke Brocker, Ekaterina Nedorubkova, Simon Voelker, and Jan Borchers. 2023. Exploring Shape Designs for Soft Robotics and Users’ Associations with Them. Extended Abstracts of the 2023 CHI Conference on Human Factors in Computing Systems. https://doi.org/10.1145/3544549.3585606
By exploring both the fabrication challenges and the aesthetic sensibilities in soft robotics, our approach creates a more integrated and holistic design process for tangible and embodied interactions. Aqua-Morph's Tangible Movement Library, based on Brocker’s [1] actuator movement categories, values aesthetic perspectives and encourages free-form exploration.
Additionally, playfulness can bridge abstract concepts and their practical applications. Modular design serves as a free agency to encourage a playful learning experience , which facilitates the exploration of variations, enabling researchers to test different geometric configurations and observe their effects on movement.
This low-cost, accessible, and reproducible DIY approach uses readily available hydrogel beads. Aqua-Morph aims to enhance the Design-HCI soft actuator toolbox, inspiring researchers to explore modular configurations, aesthetics, and emerging responsive materials.
[1] Anke Brocker, Ekaterina Nedorubkova, Simon Voelker, and Jan Borchers. 2023. Exploring Shape Designs for Soft Robotics and Users’ Associations with Them. Extended Abstracts of the 2023 CHI Conference on Human Factors in Computing Systems. https://doi.org/10.1145/3544549.3585606
EXHIBITION
2024 Dutch Design Week, Drivers of Change, Eindhoven

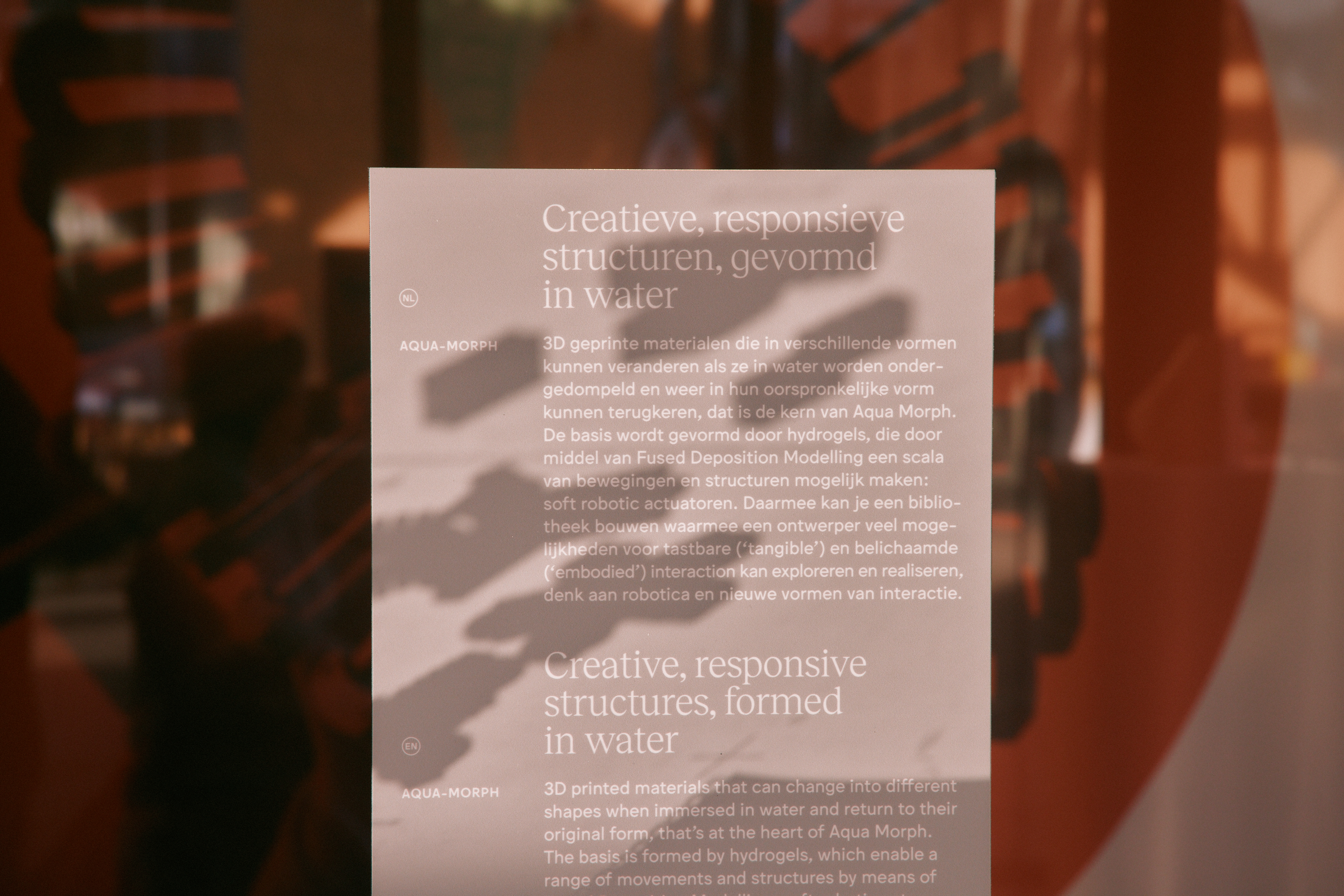
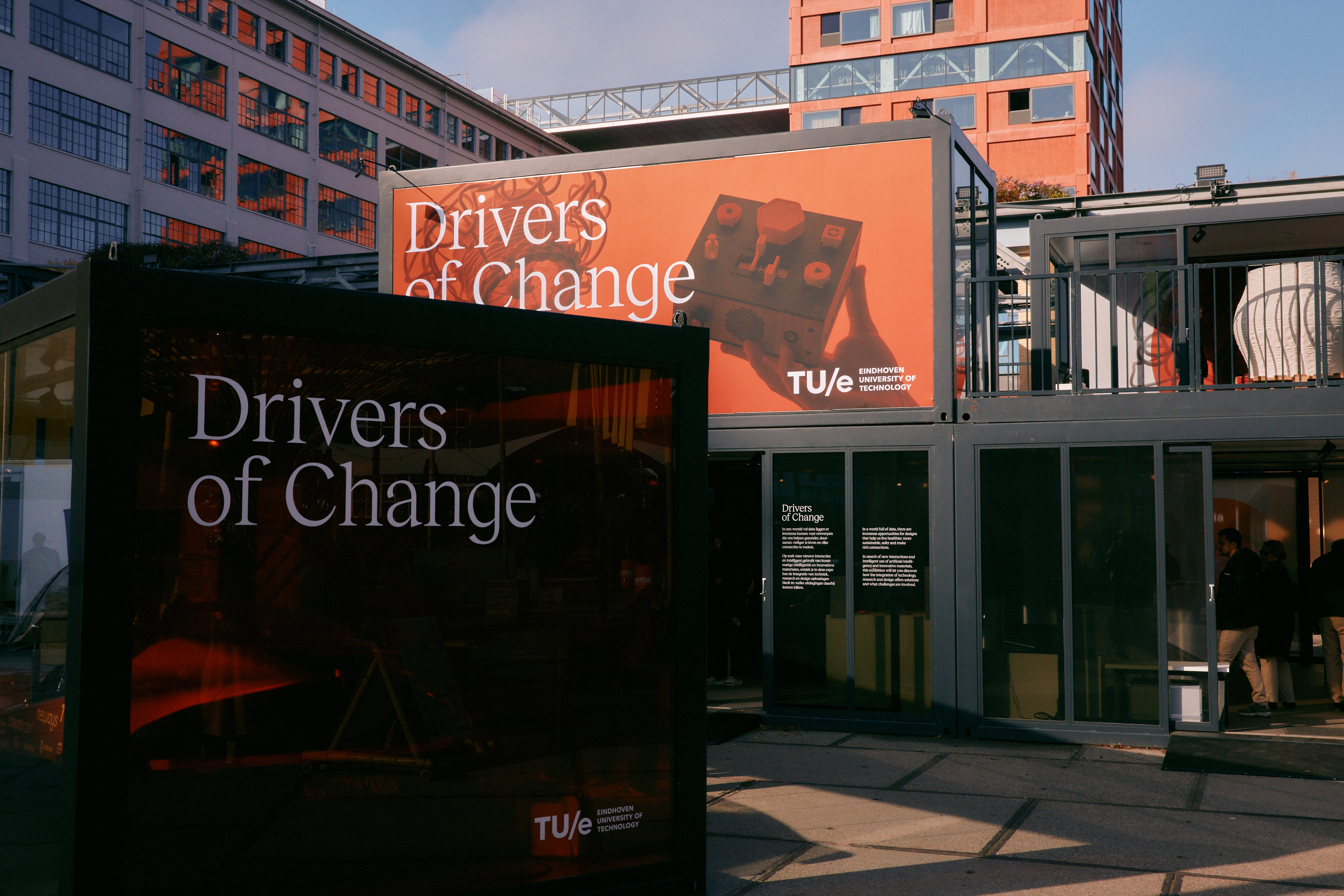